【応用編】切断後のSiCウエハの平坦化プロセスとは?研削・研磨技術について徹底解説
2025/02/13
2025/08/15
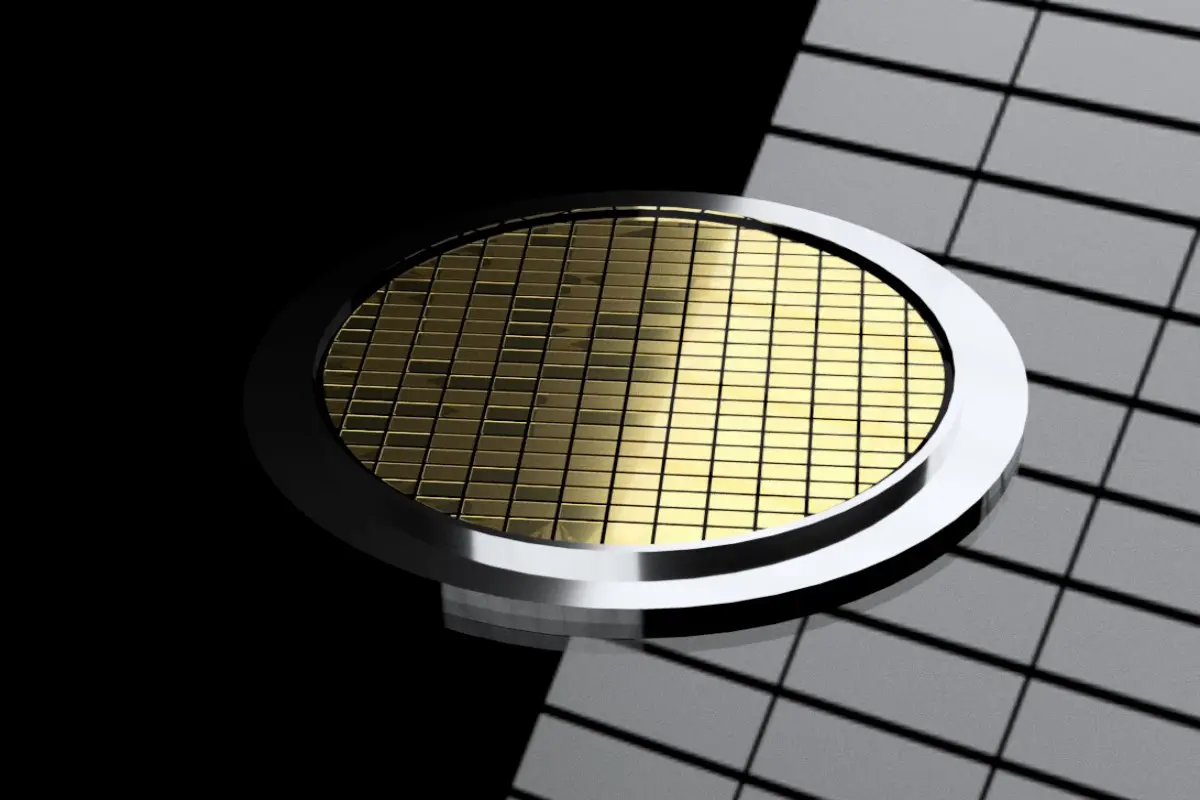
今回は、SiC半導体の基板加工の工程における「SiCウエハの研削・研磨技術」について詳しく解説します。
以下の流れで見ていきます。
- SiCウエハの研削・研磨技術の概要
- ロータリー研削
- メカニカル研磨
- 各種の援用研磨
各工程について詳しく解説していくので、是非最後までご覧ください。
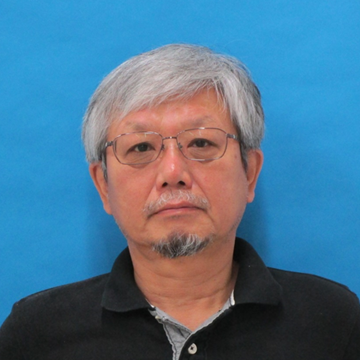
株式会社斉藤光学製作所技術顧問。専門が「研磨加工」と「微粒子分散」の技術コンサルタント。1976年、東北大学工学部を卒業後にタイホー工業株式会社 中央研究所にて磁性流体や研磨加工の研究に従事。1987年、東京大学より工学博士号(機械工学)を授与。2001年から3年間、東京大学生産技術研究所の客員教授。その後10年間は、研磨材メーカーの株式会社フジミインコーポレーテッド。さらにその後10年間は、国立研究開発法人 産業技術総合研究所 招聘研究員だった。
プロフィール詳細を見るSiCウエハの研削・研磨技術の概要
図1は、「SiC半導体とは?基板加工技術について分かりやすく徹底解説」の再掲です。
「SiCの基板加工プロセスの概要図」を示したもので、赤枠で囲んだ部分が今回の対象となります。

切断後のウエハの厚みを揃えて平行度を出してCMPに送るまでの工程、すなわち「スライスウエハの平坦加工プロセス」と呼ばれる工程です。
この工程の目的は以下になります。
- スライシングにより発生したうねりの除去、および反りの低減
- ウエハの表面粗さの低減(鏡面化)
- 前工程の加工歪の除去
現状の加工技術では、上記3つを1つの工程で行うことは難しいと言われています。
複数の工程に分け、それぞれに適した砥粒や砥石、工具を選択して加工することが必要です。
また、SiCは、熱的にも化学的にも極めて安定なため、常温ではどのような薬品を用いてもウェットエッチングは不可能です。
そのため、研削や研磨により、砥粒の粒度を細かくしていきながら徐々にダメージ層を小さくするというプロセスが必要となります。
表1は、現在実施あるいは一部で研究されている主なSiCの研削・研磨技術の種類と内容、および特徴などを、実用性の評価と共に示しています。
工程/方式 | 内容(主な研究者・企業・機関) | 特徴/実用性 | |
---|---|---|---|
ロータリー研磨 | ビトリファイドダイヤモンド砥石 | 粗研#2k~4k →精研#8k(東京精密 他) | 高レート・低ダメージ/ ◎ |
トライボ触媒砥石 | セリア等、非ダイヤモンドを用いた砥石、触媒による酸化援用効果(産総研) | 超鏡面・低ダメージ(C面のみ可)/ △ | |
メカニカル研磨 | 高硬度遊離砥粒 | ダイヤモンドラッピング・ダイヤモンドポリシング(日本エンギス他) 、B4C(産総研) | バッチ式・片面・両面/ ◎、△ |
固定砥粒定盤 | 微粒ダイヤモンド(#4k~20k)ラッピング 砥石(ミズホ 他) | バッチ式・片面・両面/ ○ | |
各種の援用研磨 | 紫外光、プラズマ、電解、熱酸化、触媒作用(産総研、各種研究機関) | 低コスト化の可能性 / ○ |
また、図2は過去に実施された国家プロジェクト「低炭素社会を実現する新材料パワー半導体プロジェクト」 (通称「FUPET」)内の応用技術調査委員会において作成されました。
SiCの研削・研磨プロセスの能率と、仕上面粗さに関するベンチマークについて表しています。

ロータリー研削技術
当時は6インチウエハがようやく出始めた時期でもあり、1枚のウエハをいかに速く加工できるかに焦点を当てた開発目標がありました。
そのため、粗加工や中間加工に相当する研削・研磨技術においては、高剛性研削盤を用いた片面ロータリー研削が最も適していたのです。
SiCは極めて硬く、ダイヤモンド砥粒を高荷重で押し込む必要があるため、ウエハ裏面を固定して片面ずつ加工する片面研削方式が有利になります。
#2,000~4,000程度のダイヤモンド砥石で粗加工した後、#8,000砥石で鏡面加工して仕上げのCMP工程に送るというプロセスが先行しました。
しかし、図3に示すように、片面毎に「枚葉加工ではウエハの貼り付けと取り外し」その後「裏返して更に貼り付けと取り外し」を行うなど、1枚を仕上げるための工数が多くなってしまうのです。
そのため量産加工には不向きという指摘もあります。
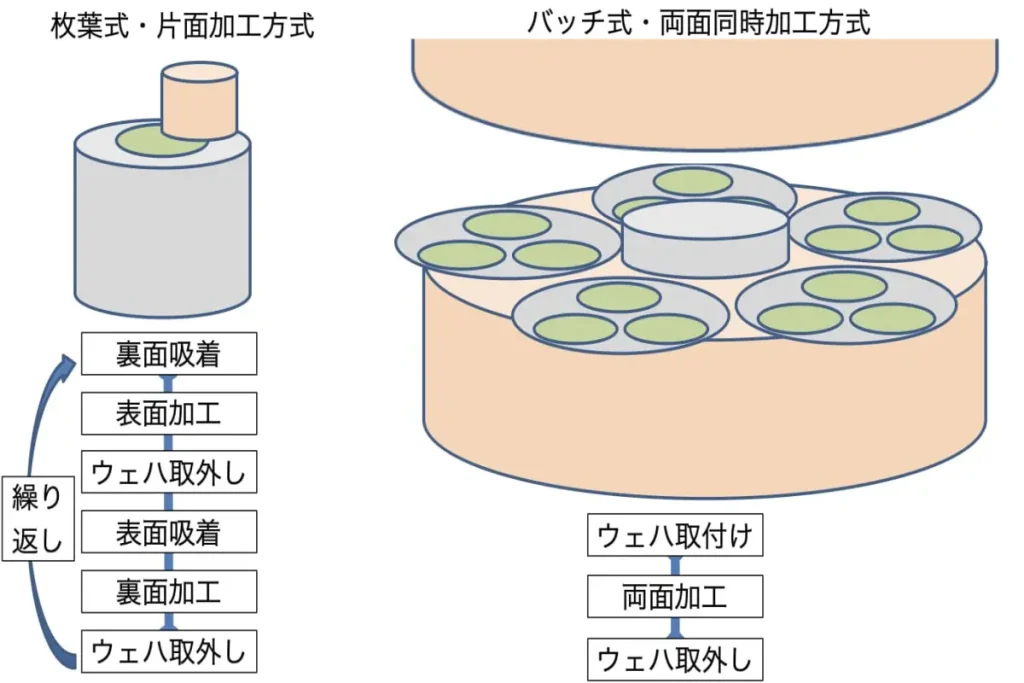
そこで、量産化への対策としては枚葉式(片面研削)から多数枚同時加工のバッチ式、更には両面同時加工へのシフトを考えることも重要となります。
以下で、表1に示す各技術について詳細に解説しましょう。
ビトリファイドダイヤモンド砥石を用いたロータリー研削技術
最初は、ダイヤモンド砥石を用いたロータリー研削です。
ロータリー研削とは、円テーブルに工作物(ウエハなど)を乗せ、工作物の上部の面に対し、テーブルを回転させて研削を行う方式です。
砥石の結合材として、一般的に使用されるのは以下になります。
- レジンボンド
- メタルボンド
- ビトリファイド
このうち、SiCに対しては主にビトリファイドが使用されています。
立型の研削盤を用いてロータリー方式でウエハを研削する事例は、Siやサファイア基板など種々のウエハ材料で実施されてきました。
しかし、SiCはそれらの材料より硬いという問題があります。
従来型研削盤の課題
図4の左側に示すような、「作用点(Working point)と力点(Power point)がオフセットしている、片持ちタイプの従来型研削盤」の場合、装置剛性が低くなります。
そのため、高番手の砥石では砥粒が滑って逃げてしまい、加工ができませんでした。
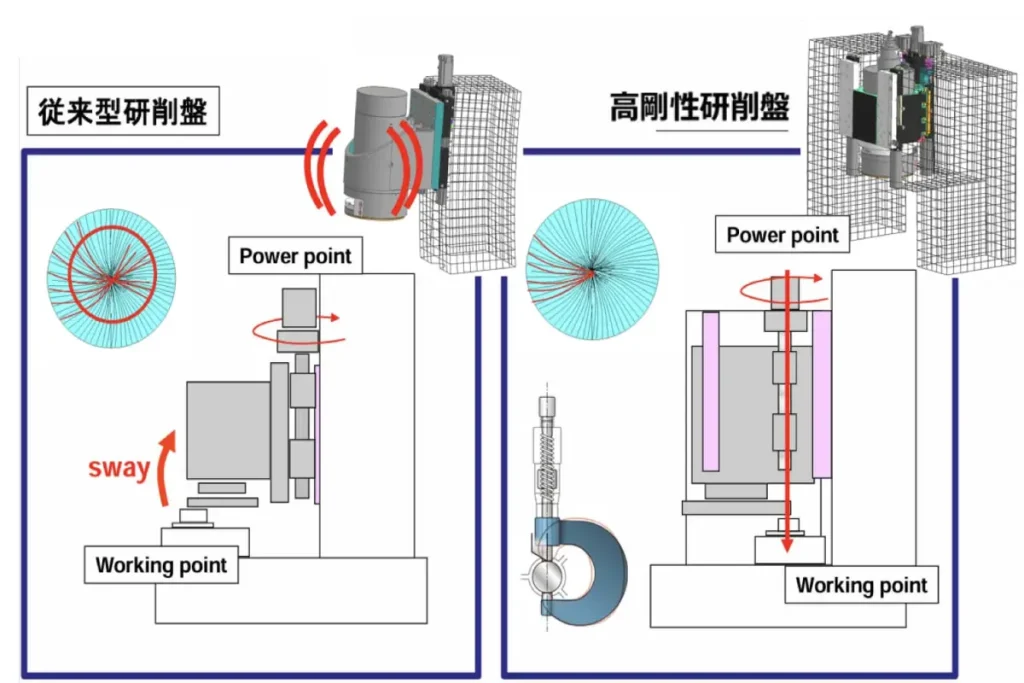
対策として、図の右側に示すような「三方からリニアガイドで囲まれた加工軸を送る、ボールねじの真下に作用点がある高剛性タイプの研削盤」が使用されます。
それにより、高番手の砥石による加工ができるようになりました。
この構造は「アッベの原理」に基づくものとなっており、送り量制御の高精度化にも役立っています。
「アッベの原理」とは
アッベの原理とは、19世紀に活躍したドイツの物理学者、エルンスト・カール・アッベが提唱した「測定精度を高めるためには、測定対象物と測定器具の目盛を測定方向の同一線上に配置しなければならない」という法則です。
アッベの原理に基づいた長さ測定器がマイクロメータで、図4の右側にマイクロメータの絵が描かれています。
それに対し、ノギスは測定点とスケールがオフセットしており、アッベの原理に従っていないので精度が悪いのです。
高剛性研削盤で可能になったこと
この高剛性研削盤では、従来型研削盤には不可能だったSiCの延性モード研削も可能になりました。
SiCは硬脆材の中でもDc値(破砕開始荷重点)が小さくなります。
そのため、延性モードで加工するには、切込み深さを常に0.15μm以下にコントロールしなければなりません。
従来型研削盤では剛性不足などのため、振動や摺動面のスティックスリップ現象(ビビリ)が起きます。
それにより送りにバラツキが生じ、結果的に切込み量が深くなってしまい、延性モード加工はできませんでした。
対応策として、高剛性研削盤では切込み量を20nm以下に調整することにより、きれいな流れ型の切り屑を作ることに成功し、延性モード加工を実現しています。
前述のFUPETの研究でも、高剛性研削盤を用い、SD#8,000砥石で6インチSiCウエハを仕上げ研削するように改良しました。
その結果、18μm/minの送り速度でRms=1nmの鏡面を実現し、ダメージ層が0.5μm以下に抑えられるようになりました。
トライボ触媒反応を利用した研削技術
SiCの研削加工にはダイヤモンド砥粒の使用が一般的です。
しかし、砥石コストおよび加工ダメージの最小化の取組みとして、ダイヤモンド以外の砥材(硬度がSiC以下の柔らかい砥材)を使った研削の可能性も検討されています。
図5は、セリアなどのSiC以下の硬度を持つ砥石で、大口径SiCウエハのロータリー研削を行った結果を示しています。
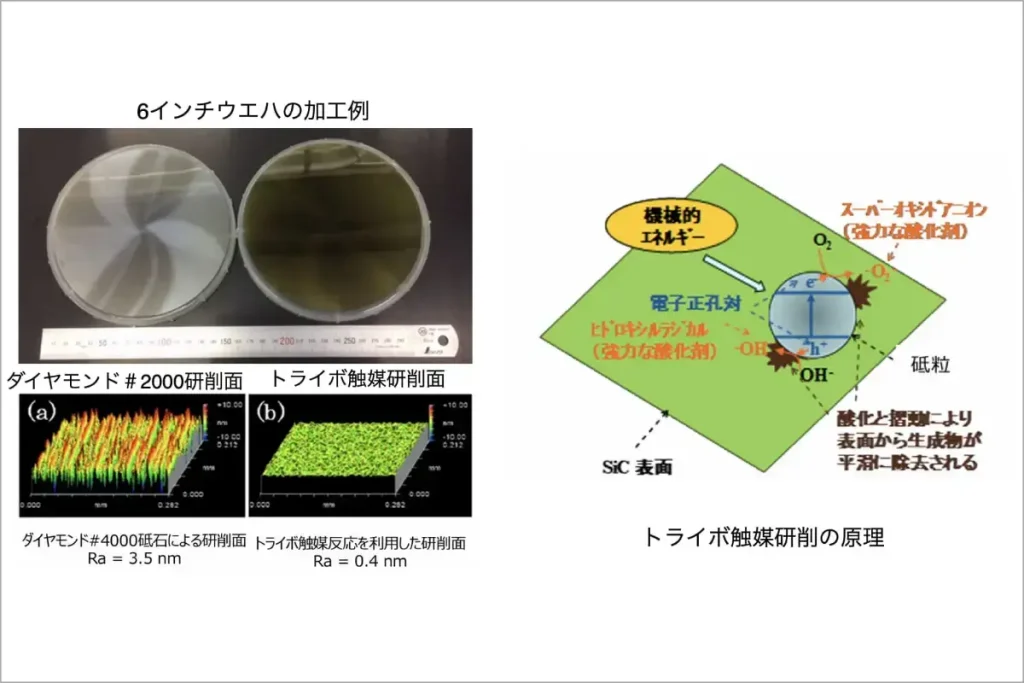
#4,000ダイヤモンド砥石で前加工した面(Ra=3.5nm)から数百nm/min以上の能率で、Ra=0.4nmの鏡面が得られます。
更には#2,000ダイヤモンド砥石で前加工した6インチウエハを、全面に渡り鏡面加工できました。
また、同図の右側に示すような加工メカニズムの考察を行い、これを利用した研削加工を「トライボ触媒研削」と名付けました 2) 。
トライボ触媒砥粒の酸化メカニズムは、光触媒のメカニズムからの類推です。
- 光エネルギーの替わりに、摺動による機械エネルギーにより、砥粒の表面近傍で電子正孔対が生成される
- 光触媒の場合と同様、電子正孔対が周囲の環境に作用して、ヒドロキシルラジカル(-OH)を生成する
- ヒドロキシルラジカル(-OH)の強力な酸化作用で、工作物であるSiC単結晶が酸化されて加工が進行する
以上のように考えられています 2) 。
ロータリー研磨によるウエハの研削加工の課題
ただし、以上の内容はウエハのC面における結果であり、同じ操作をSi面に適用しても、現状では加工できないということが分かりました。
そこで現在、産総研内の計算科学研究組織によって、酸化援用加工の反応素過程の解析と材料設計の研究が行われています 3) 。
C面とSi面でのOHラジカルの反応性の違いについて、以下のような計算結果が示されました。
- C面においては、C-O-Si構造が形成され、更にCOが解離することにより、Si-C結合が次々と切断されていく(酸化反応が進む)
- Si面においては、最表面に生成されたSi-O-Si構造が安定であるため、次の酸化反応が進まず、結果としてSi-C結合は保たれる 3)
メカニカル研磨技術
続いて、メカニカル研磨について見ていきましょう。
工程/方式 | 内容(主な研究者・企業・機関) | 特徴/実用性 | |
---|---|---|---|
ロータリー研磨 | ビトリファイドダイヤモンド砥石 | 粗研#2k~4k →精研#8k(東京精密 他) | 高レート・低ダメージ/ ◎ |
トライボ触媒砥石 | セリア等、非ダイヤモンドを用いた砥石、触媒による酸化援用効果(産総研) | 超鏡面・低ダメージ(C面のみ可)/ △ | |
メカニカル研磨 | 高硬度遊離砥粒 | ダイヤモンドラッピング・ダイヤモンドポリシング(日本エンギス他) 、B4C(産総研) | バッチ式・片面・両面/ ◎、△ |
固定砥粒定盤 | 微粒ダイヤモンド(#4k~20k)ラッピング 砥石(ミズホ 他) | バッチ式・片面・両面/ ○ | |
各種の援用研磨 | 紫外光、プラズマ、電解、熱酸化、触媒作用(産総研、各種研究機関) | 低コスト化の可能性 / ○ |
高硬度遊離砥粒を用いたメカニカル研磨技術
SiCウエハの平坦化加工方法には、前半の研削加工の他に、Siウエハで長年の実績がある遊離砥粒方式のラッピングやポリシングなどの研磨加工があります。
そして、多数枚同時のバッチ加工方式への展開や、両面同時加工の可能性を考えれば、むしろ研削加工より研磨加工のほうが実用に近いとも考えられます。
しかし、やはり工作物であるSiCの硬度がSiに比べてはるかに高いため、使用する砥粒種について検討する必要があります。
三種類の砥材を用いた加工性の比較からわかる可能性と課題
そこで、長屋ら4)は、硬度がSiC以上である三種類の砥材を用いて加工性を比較しました。
表2に示す炭化ケイ素(GC)、炭化ホウ素(B4C)、ダイヤモンドの三種類です。
砥粒種 | GC | B4C | ダイヤモンド |
---|---|---|---|
ヌープ硬度 (kg/mm2) | 2700 | 3000 | 8000 |
粒径 (μm) | 40 | 40 | 35 |
スラリー濃度 (wt%) | 15 | 15 | 1 |
スラリー流量 (mℓ/min) | 50 | 50 | 10 |
加工レート (μm/min) | 0.3 | 3.0 | 4.2 |
面粗さRms (μm) | 0.7 | 0.23 | 0.15 |
表2.SiCウエハのラッピングにおける砥粒種の影響
40μm前後という粒径は、半導体ウエハのラッピングでは普通使用されない常識外の大粒径です。
しかし「高価格のダイヤモンド以外に使用できそうな砥粒種を探す」という発想から、新しい領域での研磨加工を目指して挑戦しています。
炭化ケイ素(GC)は工作物であるSiCと同じ物質の多結晶体ですので、いわゆる「共摺り」状態となります。
そのため、加工レートは非常に低い値でした。
一方、ダイヤモンドは工作物との硬度差が倍以上ありますので、レートも高くなりました。
注目されるのは、炭化ホウ素(B4C)で、硬度差がさほどないのにレートはGCの10倍、ダイヤモンドの7割程度の値が得られた点です。
しかも、加工した面はダイヤモンド加工のような筋状の深い破砕層が無く、一様な梨地面になることが分かりました。
この結果から、切断後のうねりを両面同時ラッピングによって高速に平坦化する工程に適用できる、という可能性を示せました。
しかし、問題は炭化ホウ素の破砕性です。
破砕性が高いため切れ味は良い反面、耐久性に問題があります。
スラリーの循環使用において粒径が早期に減少し能率が急激に低下する傾向が見られました。
そのため、実用的に使用するには、もう少し検討が必要かもしれません。
片面研磨方式と両面同時研磨方式の長所と短所
次に、粗加工平坦化後の、表面粗さとダメージ層の低減工程について解説します。
SiCウエハの場合、一般的には10μm以下のダイヤモンド砥粒が使用されます。
研磨方式には「片面研磨方式」と「両面同時研磨方式」があり、各々の方式の長所・短所や、コスト・効率・表面精度などを考慮して選定する必要があります。
一般に、両面同時研磨は片面研磨と比較して切断後のうねりや反りを効率よく除去できます。
しかし、SiCウエハはSiウエハより厚さが薄いという点に注意が必要です。
SEMI規格において6インチウエハの厚さは、Siが675±20μmであるのに対し、SiCは520±20μmと
規定されています。
しかし、実際のウエハにおいては350~400μmの場合が多くなっています。
更に、キャリアプレートの厚さはウエハより薄くする必要があるため、キャリアに使用する材料の強度を考慮した加工条件を選定する必要が出てくるのです。
図6には各々の方式で使用する研磨装置を示します。
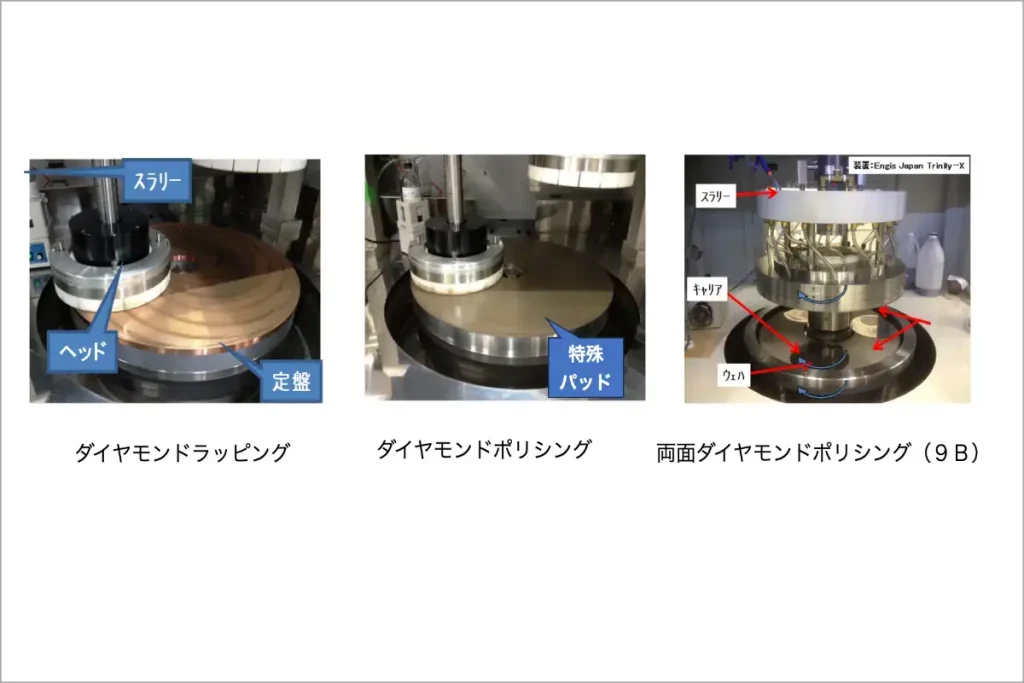
ダイヤモンドラッピングとダイヤモンドポリシングの違い
ダイヤモンドラッピングにおいて使用される工具の材質には以下があります。
- 鋳鉄
- 銅
- 錫
- 樹脂混合金属
一方、ダイヤモンドポリシングにおいては、軟質の研磨パッドを工具として使用します。
ダイヤモンドラッピングとは
片面方式のダイヤモンドラッピングでは、スラリーは間欠的に噴霧器で定盤に供給されます。
ダイヤモンド砥粒は、図7に示すようなセラミック製のリングにより、定盤に押し込まれて均一にチャージ(半固定化)されるのです。
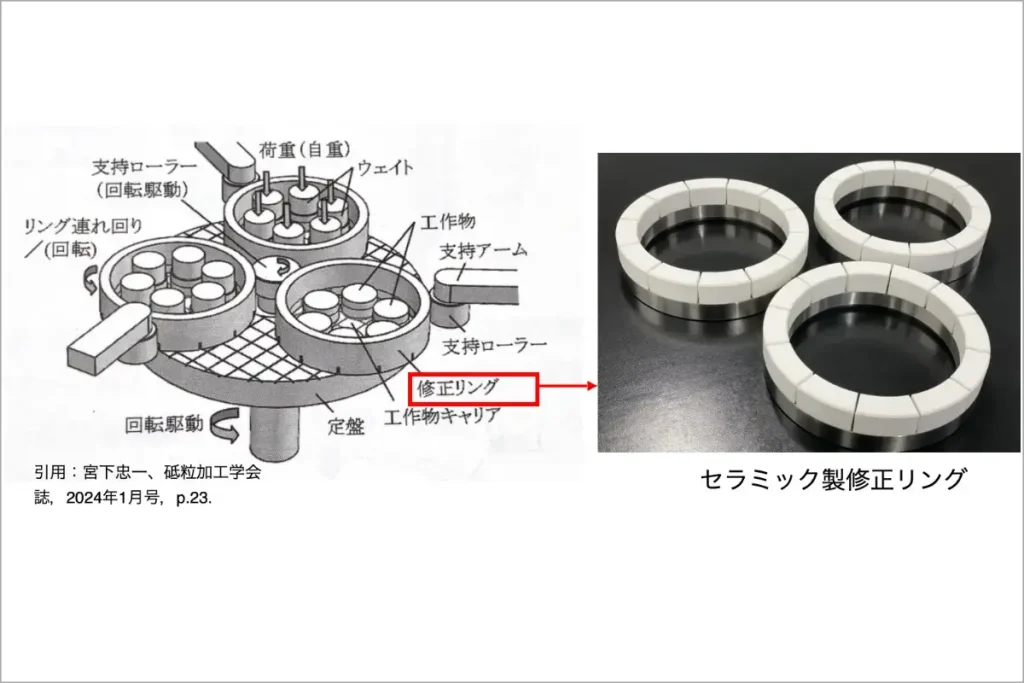
この半固定化された砥粒の先端で材料を微小切削すると共に、新たに供給される砥粒の転動作用と併用して材料除去が進みます。
半固定化された砥粒の先端は徐々に擦り減り、摩擦抵抗により脱落しますが、再び新たな砥粒がチャージされて効率良く固定砥粒化されて材量除去を継続することが可能です。
この時の研磨能率や表面粗さは、使用する定盤の硬さや、砥粒の粒径、作用砥粒数などによって変化します。
ダイヤモンドポリシングとは
ダイヤモンドポリシングは、金属定盤を用いたラッピングよりも表面粗さや加工歪を低く抑えたい時に使用されます。
方法としては、金属定盤に代わりポリシングパッドが使用される以外はラッピングと同じ構造で、材料除去のメカニズムも同様です。
金属定盤と比べて柔らかいパッドを用いるため、砥粒の突き出し量や工具への保持力が小さく、切削によるスクラッチが発生しづらくなることが期待できます。
ダイヤモンド加工とロータリー加工の比較
表3には、ダイヤモンドラッピングとダイヤモンドポリシングによるSiCウエハの加工例を、前半で示したロータリー研削の加工例と比較して示しました。
工程 | 加工面 | 工具 | 加工能率 (μm/min.) | 仕上面粗さ (nmRa) |
---|---|---|---|---|
研削 | 片面 | ビトリファイド#8000 | 18 | 1 |
ダイヤラップ | 片面 | 3μm/銅 | 1.7 | 8.4 |
ダイヤラップ | 片面 | 3μm/樹脂銅 | 1.11 | 9.2 |
ダイヤラップ | 片面 | 3μm/樹脂錫 | 0.4 | 3.6 |
ダイヤラップ | 片面 | 1μm/錫 | 0.3 | 5.6 |
ダイヤラップ | 片面 | 0.5μm/アルメット | 0.2 | 1.3 |
ダイヤラップ | 片面 | 0.25μm/アルメット | 0.1 | 1.6 |
ダイヤポリッシュ | 片面 | 3μm/パッド | 0.56 | 3.8 |
ダイヤポリッシュ | 片面 | 1μm/パッド | 0.08 | 0.61 |
ダイヤポリッシュ | 片面 | 0.25μm/パッド | 0.03 | 0.39 |
ダイヤポリッシュ | 両面 | 3μm/パッド | 0.2 | 3.8 |
表3. 各工程におけるSiCの加工能率と仕上面粗さの違い
ウエハは1水準当たり3インチを4枚同時加工(面積で6インチ相当)、加工圧40kPa、相対速度1.8m/s前後で20分加工した結果です。
ダイヤモンド砥粒は3μm以下の微細砥粒を使用していますが、ラッピングにおいても加工能率は研削に遠く及びませんでした。
ポリシングでさえも仕上面粗さを研削に近づけるのは容易ではなく、その時の能率ははるかに低いものとなっています。
しかし、ポリシングの良いところはパッドの選択により、能率と仕上面粗さのバランスを変えることができることです。
パッドの材質や構造、溝形状の改良などにより、まだまだ改善できるところがあると思われます。
研削のデメリットと、研磨の可能性
研削のデメリットとして片面ずつの枚葉加工しかできないことや、装置と砥石が高額になることです。
それに対して、以前から所有する研磨盤を使用して多数枚同時のバッチ加工ができる、というラッピングやポリシングの強みがあります。
今後は工具やスラリーや加工条件などのさらなる改良が望まれるところです。
固定砥粒(砥石)定盤を用いた研磨技術
以上のように、遊離砥粒を用いたメカニカル研磨は加工能率が低いという問題があります。
それに対して、野副ら5)は、#4,000~#20,000のダイヤモンドを使用した、固定砥粒定盤による6インチSiCウエハの鏡面研磨に取り組みました。
そして、この研磨法により従来のパッドと遊離砥粒を使ったダイヤモンドポリシングと同程度の鏡面(Ra=0.4nm)を非常に高い能率で達成できることを明らかにしています。
定盤を用いた研磨技術-1024x683.webp)
また、山本ら6)は、この固定砥粒定盤を高速研磨装置と組み合わせることで更に研磨速度が改善され、一般的な加工条件の12倍の加工能率を達成できることなどを明らかにしました。
各種のエネルギーを援用した研磨技術
高硬度のSiCに対して機械エネルギーのみに頼るのでは効率が悪いし、ダイヤモンド砥粒を使用することはやはり高コストです。
そこで、電解作用やプラズマ、紫外線と言った他のエネルギーを援用して研磨する方法が各研究機関で検討されています。
陽極酸化反応を利用したSiCの電解研磨
脱ダイヤモンドを目指して筆者ら7),8)が取り組んできたのが、陽極酸化反応を利用したSiCの電解研磨です。
SiCの陽極酸化を利用した電解研磨の研究は以前から行われています9)が、実用サイズのウエハを効率よく鏡面研磨できる量産加工技術としては未だ確立されていません。
私たちの目的は、この研磨法の実用化にあるため、6インチウエハに対応できる電解研磨装置(図9)を新たに開発して研究を進めてきました。
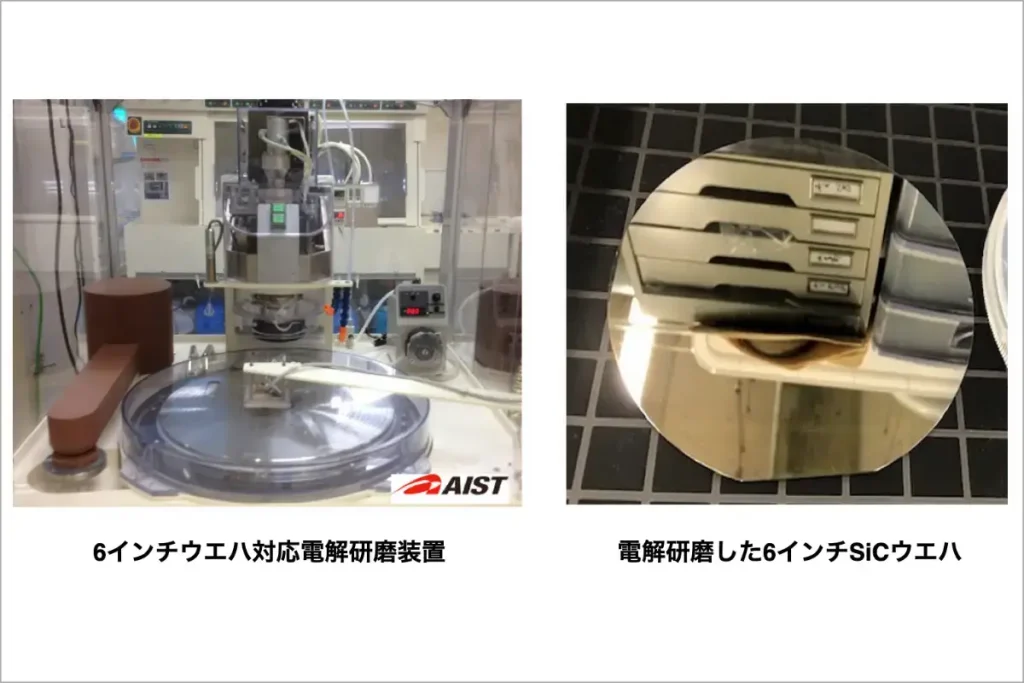
この方法の詳細については、別途改めてお伝えしますのでお楽しみに。
以上、今回はSiCウエハの研削・研磨技術について解説いたしました。
次回は、「SiCウエハのCMP技術」について解説します。
参考文献
1)五十嵐健二:「シリコンと化合物半導体の超精密・微細加工プロセス技術 第12章 高剛性研削盤による難削材の最先端加工技術」,株式会社シーエムシー出版, (2024.06), 126.
2)T.Kido et al.“A novel grinding technique for 4H-SiC single crystal wafers using tribo-catalytic abrasives wheels “, Mater. Sci. Forum, 778(2014),754.
3)M.Kayanuma et al. Surface Science, 791, 122031(2021)
4)長屋正武ら:「SiC半導体ウエハの加工技術」,デンソーテクニカルレビュー,vol.20,(2015)222.
5)野副厚訓ら:「固定砥粒ラップ定盤による大口径SiCの研磨プロセスの開発」,先進パワー半導体分科会誌第9回講演会予稿集,9,1(2022)105.
6)山本悠子ら:「高速研磨装置と砥石定盤を用いた SiC ウェハの高レート研磨技術」,先進パワー半導体分科会誌第9回講演会予稿集,9,1(2022)107.
7)河田研治ら:「陽極酸化を利用したSiCウエハの高能率電気化学機械研磨(ECMP)法の開発-断面TEMによる加工歪の評価-」, ABTEC2021講演論文集,A06(2021)
8)河田研治ら:「陽極酸化を利用した SiC ウエハの高能率電気化学機械研磨(ECMP)法の開発(第2報)-表面粗さの形成メカニズム-」,ABTEC2022講演論文集,D15 (2022)
9)Canhua Li et al., ; Electro-Chemical Mechanical Polishing of Silicon Carbide, Journal of Electronic Materials, 33, 5(2004)481.