【応用編】SiCウエハ加工の最終工程「CMP技術」とは?現在の技術から将来性まで徹底解説
2025/04/10
2025/08/15
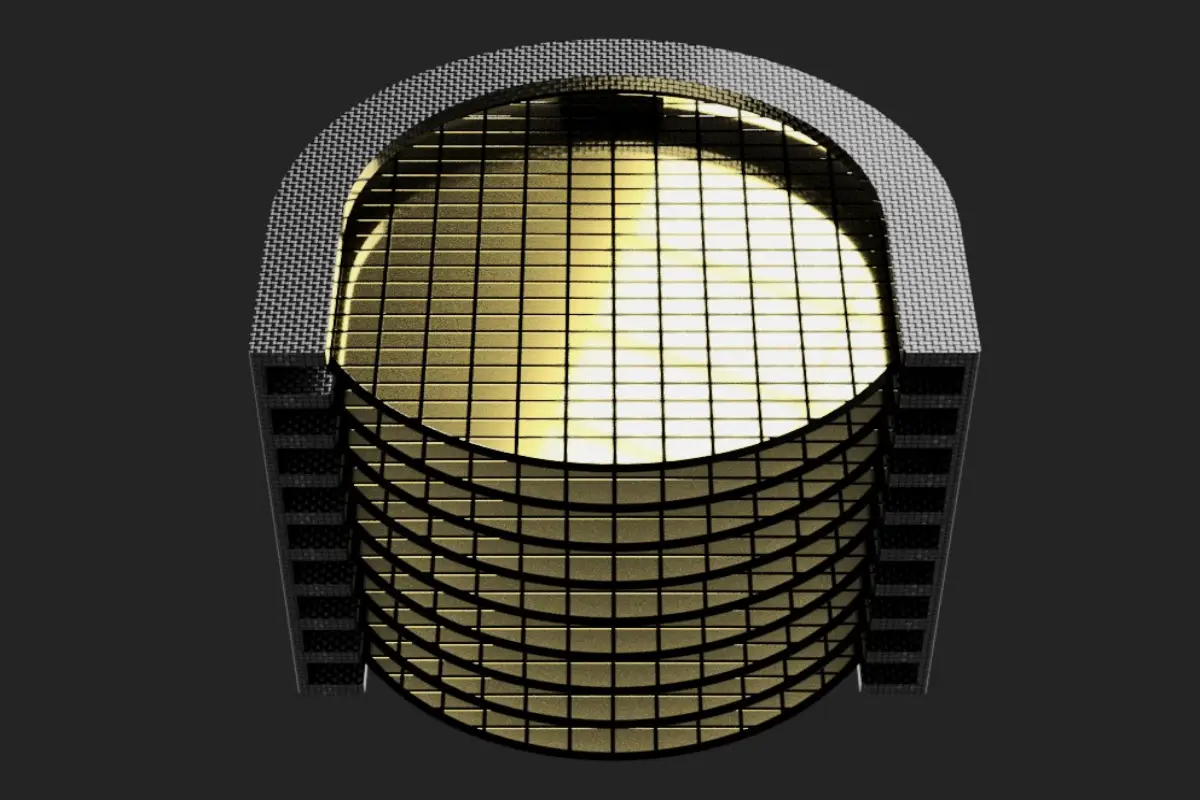
今回は、SiCウエハ加工の最終工程となる「CMP(Chemical-Mechanical Polishing)技術」について解説いたします。
SiC半導体の基板加工の基礎に関しては「SiC半導体とは?基板加工技術について分かりやすく徹底解説」の記事で解説していますので、そちらもご参照ください。
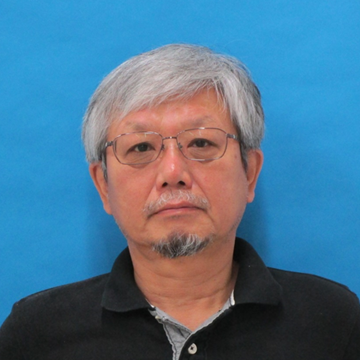
株式会社斉藤光学製作所技術顧問。専門が「研磨加工」と「微粒子分散」の技術コンサルタント。1976年、東北大学工学部を卒業後にタイホー工業株式会社 中央研究所にて磁性流体や研磨加工の研究に従事。1987年、東京大学より工学博士号(機械工学)を授与。2001年から3年間、東京大学生産技術研究所の客員教授。その後10年間は、研磨材メーカーの株式会社フジミインコーポレーテッド。さらにその後10年間は、国立研究開発法人 産業技術総合研究所 招聘研究員だった。
プロフィール詳細を見るSiCウエハのCMP技術の概要
前回の記事「切断後のSiCウエハの平坦化プロセスとは?研削・研磨技術について徹底解説」でも述べたように、CMPの前工程では、主に砥粒としてダイヤモンドが使用されます。
しかし、ダイヤモンドによる加工は、如何に小さい粒子を使用したとしても加工歪(ダメージ)を発生させます。
半導体材料の表面は、数十ナノメートルという極表層のダメージの残存がデバイス特性を著しく劣化させてしまうため、最表面まで単結晶状態であることが必要です。
Siを含め、これまで半導体材料の最終研磨工程には、一般的にCMPが使用されてきました。
これはCMPが砥粒の機械的作用のみでなく化学的作用とのバランスにより加工を進行させ、無歪み・無欠陥仕上げを実現できるためです。
同時に、操作も簡便で、コストも比較的安く、大量生産に適していることも理由の一つになります。
SiC研磨の基礎
ここで、SiC研磨の基礎についておさらいしておきましょう。
SiC研磨の研磨方法
CMPの操作方法は、Siの場合と同様です。
研磨定盤に貼り付けられた研磨パッド上にCMPスラリーを流し、研磨定盤にSiCウエハを押し付けながら、研磨定盤とウエハとをそれぞれ回転させて行います。
CMPにおいては、遊離砥粒による機械的除去作用を化学作用がアシストすることで、高精度な表面を効率的に得られます。
SiCの場合の化学作用としては、SiCの酸化反応が利用され、以下の方法で高い研磨能率を実現しています1)。
- 高硬度のSiCをSiO2あるいはSi-Oなどのアモルファスに変換して軟質化する
- SiCの強固な共有結合との電子の授受により結合力を弱める
SiC用CMPスラリーの構成
SiC用のCMPスラリーは純水をベースとして砥粒と酸化剤で構成されるのが一般的です。
砥粒としてはアルミナやシリカが用いられることが多く、稀に酸化クロムや酸化マンガンが使用されることもあります。
酸化クロムはSiCやSi3N4、AlNなどに対するメカノケミカル効果が高く注目されましたが、環境への配慮から現在は使用が控えられています。
CMPスラリーにおいては、機械的作用を付与する砥粒と、化学作用を付与する酸化剤の配合比のバランスが大変重要です。
機械的作用が勝れば研磨面の平坦度が良好となりますが、ダメージは発生しやすくなります。
一方、化学作用が勝れば研磨能率は高くなりますが、エッチングによる表面荒れや不均一な凹凸が発生しやすくなります。
つまり、十分な平滑度や平面度が得られにくくなるといった問題が発生するのです。
そのため、高能率を目的とする場合は、機械的作用が強いアルミナ砥粒と化学作用が強い強酸化剤が組み合わされます。
また、高精度を目的とする場合は、機械的作用が弱いコロイダルシリカと化学作用が緩やかな触媒型酸化剤が組み合わされているのです1)。
以後においては、前者を「強酸化剤型スラリー」、後者を「触媒反応型スラリー」と呼ぶことにします。
研磨の最終目的
CMP後のウエハは洗浄され、エピレディウエハとなって次工程のエピタキシャル成長に進みます。
そこでSiC層が成膜され、その後デバイス工程へと進むのです。
その際、エピタキシャル成長はウエハの表面形状や結晶のダメージを引き継ぎながら成長していきます。
そのため、最終的にエピレディウエハの表面品質がエピ後の欠陥密度や表面精度に大きな影響を及ぼすこととなります。
したがって、エピレディウエハには高い平滑度や平坦度、無欠陥や無汚染が求められるのです。
究極的には、原子レベルの平坦性、および無擾乱の結晶性が求められます。
CMPによる原子レベルの平坦性の実現
のAFM像-1024x683.webp)
図1に示すのは以下の内容の測定結果です。
- 4H-SiCウエハ(on-axis:オフ角が0度)の(0001)Si面について
- 一般的なアルカリ性コロイダルシリカスラリー及び、SiC専用の研磨剤スラリー(触媒反応型スラリー)で研磨した面の原子間力顕微鏡(AFM)による測定結果
一般的なアルカリ性コロイダルシリカで研磨した面は、多くのピットが発生しています。
一方、SiC専用スラリーで研磨した面では、表面粗さ(Ra)は0.1nm以下の非常に平滑な面が得られます。
また、AFM像から、原子ステップが規則正しく配列している様子も観察できました2)。
原子ステップは、結晶面と研磨面のわずかなずれによって生じる表面構造です。
規則正しい原子ステップの形成は、SiCがCMPにより最表面まで結晶性を保った状態で平滑化されていることを示しています。
なお、原子ステップの高さが、Si-C結合一周期分である約0.25nmであることも確認されました2)。

図2には、(0001)Si面および、それ以外の(000-1)C面、(1-120)A面、(1-100)M面について研磨した結果を示します。
従来の研磨剤ではピット発生により正常なCMPが困難でしたが、C面においてもSi面同様の原子ステップが観察されています。
さらに、Si面とC面の間に存在するA面やM面についても同様にRaが0.1nm以下となることが分かりました。
また、研磨能率については、Si面が最も低く、C面は5倍以上高いことが分かります。
その理由は、前回の記事「切断後のSiCウエハの平坦化プロセスとは?研削・研磨技術について徹底解説」で述べたように、Si面とC面におけるOHラジカルとの反応性の違いによるSi-C結合の切断速度の差によるものと考えられます。
同様に、研磨能率がC面>M面>A面となっているのは、結晶面に現れるSi原子とC原子の比率によるものです。
強酸化剤型スラリーと触媒反応型スラリーの研磨性能の比較
SiCのCMPにおいては、最表面まで単結晶性を保った原子レベルの平坦性が得られることが最重要です。
その次に、短時間でこの超平坦面が達成できることが求められます。
そこで、触媒反応型スラリーと、強酸化剤型スラリーの性能を比較しました3)。
その結果、図3に示すように、研磨能率においては触媒反応型スラリーの10倍以上高い能率が強酸化剤型スラリーにより得られました。
その時の仕上げ面粗さは、触媒反応型スラリーが若干良好ですが、どちらもエピレディウエハに必要とされるRms≦0.1nmは満たしています。

次に、加工面の評価を以下の方法で行いました。
- コンフォーカル微分干渉顕微鏡(CDIOM)
- 放射光X線トポグラフィー(SXRT)
- 原子間力顕微鏡(AFM)
最終仕上げ面の評価指標として、最近はウエハ表面のモフォロジーをCDIOMで観察して、線状の欠陥(スクラッチ)が認められた場合、あるいは表面下のダメージをSXRTで観察します。
また、線状の欠陥(潜傷)が認められた場合には、エピ工程でステップバンチングが発生し、デバイス工程での歩留まりを劣化させることが分かっています4)~8)。
そこで、これらの評価を強酸化剤型スラリーでCMP仕上げしたウエハに対して行いました。
結果の一例を図4に示しますが、CDIOM、SXRTともにウエハ全面にわたり線状の欠陥は認められませんでした。
また、AFMによる粗さの測定例を同図に示しますが、ウエハ内で5点測定し全てRms≦0.1nmを満たしています。

さらに、次工程であるエピ工程への影響を調べるために、高温水素による気相エッチング後の表面の違いを調査しました。
この処理で発生するステップバンチングが一定レベル以下に抑えられれば、エピレディ面として適用可能であることを実証できると考えられます。
図5は、触媒反応型スラリーで仕上げた面と、強酸化剤型スラリーのみで仕上げた面の気相エッチング後の表面のCDIOM像です。

触媒反応型スラリーで仕上げた面はバンチドステップの数が少なく、エピタキシャル成長後も市販エピレディウエハをも凌ぐ良好なエピ膜が得られることが確認されています9)。
一方、強酸化剤型スラリーのみで研磨した面は、バンチドステップの線密度が一桁以上高く、エピレディ面の品質には至っていないことが示されました。
二段CMPプロセスの検討
以上の結果から、強酸化剤型スラリーのみを用いたプロセスでは、エピレディウエハとすることは困難であることが分かりました。
そこで、強酸化剤型スラリーを用いた高速プロセスを一研に適用し、エピまで実績のある触媒反応型スラリーによる高面品質プロセスを二研に適用する二段プロセスを検討しました。
実験したプロセス条件と表面性状の評価結果を表1に示します。
評価結果から、CDIOMとSXRTにおいてはどちらも線状欠陥が観察されず問題ありませんでした。
プロセス条件 | 評価結果 | |||||||
---|---|---|---|---|---|---|---|---|
一研(強酸化剤型スラリー) | 二研(触媒反応型スラリー) | CDIOM | SXRT | AFM(10μm口) | ||||
加工時間 min | 取り代 μm | 加工時間 min | 取り代 μm | 〇: 線状 欠陥なし | 〇: 線状 欠陥なし | Rms nm | Ra nm | |
A (一研のみ) | 10 | 1.5 | 0 | 0 | ○ | ○ | 0.11 | 0.08 |
B | 10 | 1.1 | 10 | 0.02 | ○ | ○ | 0.06 | 0.05 |
C | 10 | 0.7 | 30 | 0.06 | ○ | ○ | 0.06 | 0.05 |
D | 10 | 1 | 60 | 0.12 | ○ | ○ | 0.07 | 0.05 |
E (二研のみ) | 0 | 0 | 300 | 0.9 | ○ | ○ | 0.07 | 0.06 |
一方、AFMによる表面粗さは、一研仕上げ面は、Rmsがほぼ0.1 nm程度です。
しかし、二研まで実施した面はいずれも現行プロセス同等のRms値まで向上することが分かりました。

また、図6は、二研の研磨時間によるAFM表面粗さの変化を示したものです。
10分程度の二研で、ほぼ現行プロセス同等の粗さとなります。
そのため、現行(二研のみ)のプロセス時間に比べ大幅な時間短縮が可能となりました。
但し、0.1nm以下の値はAFMの感度限界とも考えられます。
そこで、電子をプローブとし、表面の静電ポテンシャルをマッピングする最新の手法、ミラー電子顕微鏡10)を用いた評価を実施しました。

図7には、表1の各ウエハについてミラー顕微鏡を用いた評価を行った結果の一例を示しました。
ミラー電子顕微鏡は、研磨表面近傍に浅く内在する潜傷や、数nmオーダー幅、深さの微小なスクラッチ、ピットなどを非常に高感度に検出できるといわれています。
実際にCDIOMやSXRTでは現れなかった差が見られています。
ウエハA(一研のみ)では全面に白い線(表面が凹)が見られ、表面に存在する微小スクラッチの存在が明らかとなりました。
それに対し、二研を実施したウエハB~E(二研のみ)については、ウエハAとは明らかな差が見られ、二研の研磨時間に比例し、面品質は向上することが分かっています。
図6と図7の結果から、一研後、二研を10分以上実施すれば、表面モフォロジーがほぼ同等になると推測できます。
CMPプロセスの世界の現状と将来予測
以上のように、SiCウエハの最終仕上げとなるCMPプロセスにおいては以下のことが分かりました。
最も短時間で高精度かつ無擾乱な研磨面を得るための方法は、多段のCMPプロセスです。
- 高能率な強酸化剤型アルミナスラリー
- 高い品質の仕上面が得られる触媒反応型シリカスラリー
こちらの2つの組み合わせになります。
しかしながら、実際のプロセスでは必ずしも多段プロセスが用いられているわけではありません。
基板品質を重要視するアジアのメーカーにおいては、現在も多段プロセスが多く採用されています。
しかし、圧倒的な基板シェアを有する欧米のメーカーでは、強酸化剤型だけの単独プロセスが主流となっています1)。
また、研磨の方式も従来のバッチ式から、枚様式へと移行する傾向にあります1)。
枚様式のほうが高負荷の加工条件で実施できるため、今後の更なるウエハ大口径化に対応しやすいという考え方からのようです。
一方で、主流となりつつある強酸化剤型スラリーの排水処理対策には、一部で懸念を持たれています。
強酸化剤である過マンガン酸塩の排水基準や環境基準は非常に厳しく、現状でも処理に高いコストが掛かっているからです。
そのため、スラリーメーカーにはスラリーの繰り返し使用やリサイクル、低濃度化など「低CoO化(総合的なコストを抑えるための商品設計)」が求められています。
並行して、環境に配慮したスラリーの開発なども進めていく必要があります。
また,人体や環境への影響を考えると、強酸化剤による化学的な酸化力の代わりになるエネルギーが求められます。
- 電解作用(陽極酸化)
- プラズマ
- 紫外線
このような他のエネルギーを援用して、最終仕上げする方法の構築も望まれています。
参考文献
1) 高見信一郎:「シリコンと化合物半導体の超精密・微細加工プロセス技術 第22章 SiC半導体のCMPとポリシングの課題」,株式会社シーエムシー出版, (2024.06), 229.
2) 堀田和利ら:「コロイダルシリカによるSiC単結晶基板の高品質加工」,2007年度精密工学会春季大会学術講演会講演論文集、M21,(2007)1145.
3) 河田研治ら:「パワーエレクトロニクス用SiCウエハの高能率CMPプロセスの開発」,2015年度砥粒加工学会学術講演会講演論文集(2015)367.
4) H. Sako et al., Microstructural analysis of damaged layer introduced during chemo-mechanical polishing, Materials Science Forum Vols. 778-780 (2014) 370.
5) M. Sasaki et al., Analysis on generation of localized step-bunchings on 4H-SiC(0001)Si face by synchrotron X-ray topography, Materials Science Forum Vols. 778-780 (2014) 398.
6) M. Kitabatake et al., Electrical Characteristics/Reliability Affected by Defects Analyzed by the Integrated Evaluation Platform for SiC epitaxial films, Materials Science Forum Vols. 778-780 (2014)979.
7) K. Yamada et al., Reliability of gate oxides on 4H-SiC epitaxial surface planarized by CMP treatment, Materials Science Forum Vols. 778-780 (2014) 545.
8) J. Sameshima et al., Relation between defects on 4H-SiC epitaxial surface and gate oxide reliability, Materials Science Forum Vols. 740-742 (2013)745.
9) 長屋正武ら:「6インチSiCウエハの一貫加工プロセス」,低炭素社会を実現する新材料パワー半導体プロジェクト 最終成果報告会 ポスター要約集(2015)16.
10) 品田博之ら:「次世代の高速高感度検査 -ミラー顕微鏡技術の可能性-」,日立評論Vol.94 No.02 (2012.02)46.