【応用編】インゴット切断とは?SiC半導体の基板加工について解説
2024/12/27
2025/08/15
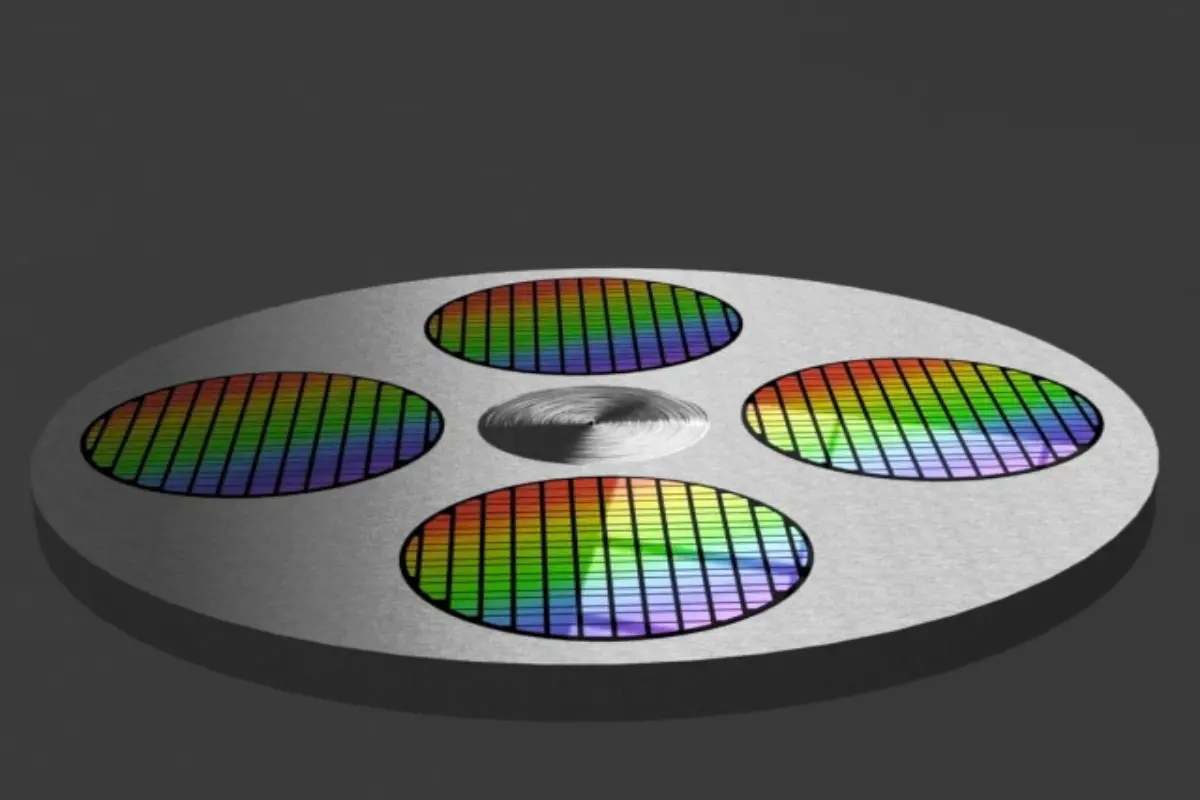
今回は、SiC半導体の基板加工技術の応用編を徹底解説いたします。
SiC半導体の基板加工の基礎に関しては「SiC半導体とは?基板加工技術について分かりやすく徹底解説」の記事で解説していますので、そちらもご参照ください。
最近注目を集めている、インゴッド切断技術の種類と特徴について詳しく解説していきます。
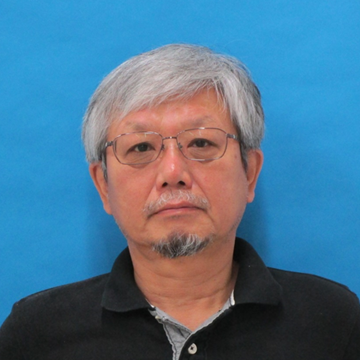
株式会社斉藤光学製作所技術顧問。専門が「研磨加工」と「微粒子分散」の技術コンサルタント。1976年、東北大学工学部を卒業後にタイホー工業株式会社 中央研究所にて磁性流体や研磨加工の研究に従事。1987年、東京大学より工学博士号(機械工学)を授与。2001年から3年間、東京大学生産技術研究所の客員教授。その後10年間は、研磨材メーカーの株式会社フジミインコーポレーテッド。さらにその後10年間は、国立研究開発法人 産業技術総合研究所 招聘研究員だった。
プロフィール詳細を見るインゴッド切断技術の概要
単結晶炭化ケイ素(SiC)インゴットの切断技術にはいくつかの方法があります。
主な方法は図1に示す通りです。

大きく分けると、以下の2つに分かれます。
- 多数枚を同時に切り出すバッチ式
- 一枚ずつ切り出す枚葉式
バッチ式について
バッチ式の代表はマルチワイヤソーです。
マルチワイヤソーには、ダイヤモンド砥粒を分散したスラリーを用いた遊離砥粒方式と、ダイヤモンド砥粒をワイヤに固着したダイヤモンドワイヤを用いた固定砥粒方式があります。
また、ダイヤモンドを使用しない方法として放電加工を利用したマルチ放電スライシングがあります。
枚葉式について
枚葉式の切断方式としてはレーザ光を利用したレーザスライシングがあります。
以下では、それぞれの方式について詳細に解説しましょう。
インゴッド切断技術の種類と特徴
マルチワイヤソーについて
マルチワイヤソーは、ムーアの法則にしたがって大口径化したシリコンインゴットに対応するため、1980年代中頃から注目されるようになりました1)。
それまで使用された外周刃方式よりも加工速度は遅いですが多数枚同時(マルチ)に切断することによる採算性の高さが評価されました。
現在ではシリコン、GaN、サファイア、SiCの基板加工に用いられています1)。
マルチワイヤソー装置の概要を図2に示しました。

マルチワイヤソーは、スピンドルヘッドに組み込まれた2~4本の切断用ガイドプーリー(ガイドローラー)を備えています。
そのガイドプーリーには、一定間隔で複数の溝が掘られています。
一本の切断用ワイヤを各ガイドプーリーの溝外周に順に巻きつけることで、マルチ刃の切断機とする構造です。
切断加工はガイドプーリーに巻きつけたワイヤに対し、垂直に単結晶インゴットを押し当てます。
ワイヤが一定の張力を保ちながら左右往復走行することで、ウエハ形状に切断されるのです。
1.遊離砥粒方式のマルチワイヤソーとは
遊離砥粒方式のマルチワイヤソーにおいては、エチレングリコールなどを配合したベース液に、5~10μm程度の単結晶ダイヤモンド砥粒を懸濁させたスラリーを、工具となるピアノ線ワイヤに流しかけながら加工を行います。
ワイヤ径は通常180μm前後のものが使用されます。しかし、最近はカーフロス(切り代)を小さくして材料を有効に使うため、より細い100~125μmのワイヤが使える装置も出てきています。
この方式における砥粒の作用機構としては、ダイヤモンド砥粒が工作物と工具との間で転動しながら工作物を除去するメカニズムです。
そのため、脆性モードの加工となり切断面は梨地となります。
最近は、ポリウレタン系の樹脂をコーティングしたワイヤにより延性モード加工を実現した例も報告されています1)。
遊離砥粒方式は時間がかかりますが、ワークに与えるダメージが少なく、比較的良好な切断面が得られる方法として現在も広く使用されているのです。
2.固定砥粒を用いたマルチワイヤソーとは
ダイヤモンドを電着したワイヤで切断する方式です。
SiCウエハの大口径化が進むにつれ、遊離砥粒方式では、インゴットの中心付近になるとスラリーが切溝に入りづらくなるという問題が生じてきました。
また、高速切断への要求もさらに高まります。
そこで、切断速度の遅い遊離砥粒に代えて、高能率が見込める電着ダイヤモンドワイヤを用いた固定砥粒方式の切断技術の開発が進んできたのです。
6インチサイズのSiCインゴットが出始めた2010年頃、遊離砥粒方式のマルチワイヤソーでは切り出しに100時間以上かかると見込まれました。
そのため、当時の国家プロジェクト(『低炭素社会を実現する新材料パワー半導体プロジェクト』、通称FUPET)において、高速切断を目指します。
電着ダイヤモンドワイヤの線速を従来の3~4倍に高めたマルチワイヤソーで十分の一以下の9時間で切断できることが示されました。
また同時に、線速が高いほど切断ウエハの反りが小さくなることが示されたのです2)。
この時のダイヤモンドワイヤは、180μm径の芯線に30~40μmサイズのダイヤモンドを電着したものです。
ワイヤ径が250μmほどあったため、カーフロスが大きいことが問題でした。
また、以下3点が原因となる、ワイヤコストの増加が課題として残ります。
- 高線速化による加工熱
- 残留応力の増大
- ワイヤ使用量の増大
しかしその後、高精度ワイヤ送り制御や、ワイヤの細線化・砥粒の細粒化などの改善が図られます。
その結果現在では、ワイヤ径も150μm程度にまで抑えられるようになりました。
また、ワイヤ走行性の向上により、加工熱や残留応力への対応も進んできています。
3.マルチワイヤ放電スライシング
放電加工でSiCを切断する技術も進んでいます。
放電加工とは雷と同じ現象を人工的に連続発生させ除去加工を行う方法です。
パワー半導体に使用するn型SiCの電気抵抗率は0.1Ωcm以下であるため、充分に放電加工が可能なのです。
マルチワイヤ放電スライス加工機の概要を図3に示しました。

装置的には、マルチワイヤソーと同様に、1本のワイヤを各ガイドローラーの溝外周に順に巻きつけることで、マルチの切断機とする構造になっています。
巻きつけた各々のワイヤで放電を同時に発生させることのできる「マルチ加工電源」を開発し、一度に切り出せるようにしています。
SiCインゴットを機械的に切断しようとすると、使用できる砥粒は価格の高いダイヤモンドのみで高コストが避けられません。
しかし、放電加工の場合、消耗品は真鍮などの金属ワイヤのみで、ランニングコストの大幅な低減が図れます。
現在では、6インチ径のSiC単結晶に対して20並列電源を使用し、20枚同時加工を行うこともできるのです。
ワイヤ電極径100μm、ワイヤピッチ600μmで、加工時間36.5時間で切断した実績があります3)。
以上の3つの方式は、多数枚同時に処理するバッチ式加工です。
次に解説するレーザスライシングは一枚ずつ切断する枚様式加工になります。
4.レーザスライシング
単結晶SiCインゴッドのレーザスライシングの原理を図4に示しました。

SiC単結晶の内部でレーザを集光させるとSiCは熱分解してアモルファスSiとCに解離します。
この時、体積膨張が生じて内部の引張応力でへき開面に沿って亀裂が発生します。
レーザ走査により、へき開を進展させるようにレーザを複数照射して、へき開を連結させます。
全面にへき開が生じた後、何らかの方法で上下に剥離すれば切断が完了するのです。
ただし、現在主流の基板はへき開面(0001)と4°ずれているため、剥離面はまるで洗濯板のように整然とした凹凸の縞模様が形成されます。
そのため、図4の右端の図のように、凹凸部分+10μm程度を鏡面研削しないと、次のレーザ光を透過させられません。
そこで、片側数十μm、上下合わせて100μm位がウエハ1枚当たりで、材料ロスが生じることになります。
まとめ
以下の表1は、固定砥粒方式マルチワイヤソーとレーザスライシングについての比較です。
「インゴット長を20mm、切断・研削後のウエハ厚0.35mm」とした時の、取れ数と1枚当たりの加工時間をそれぞれ比べています。
切断方式 | レーザスライシング(枚葉式) | マルチワイヤソー(バッチ式) |
---|---|---|
取れ数(枚) | 44 | 28 |
合計の切断時間 | 25分×44=18時間20分 | 4時間 |
1枚あたりの切断時間 | 25分(照射5分、剥離5分、研磨15分) | 8分40秒 |
切断・研磨後の材料ロス率 | 22% | 49% |
※インゴット長20mm、切断・研磨後のウエハ厚0.35mmとした
赤文字の項目が相手に対して優位な点
レーザスライシングの最大の長所はワイヤソーのようなカーフロスがなく、インゴットからのウエハの取れ数(収率)の大幅な増加です。
よって、将来的には、結晶成長が長尺化・高速化してインゴットが安くなれば、現状の固定砥粒方式マルチワイヤソーが量産には向いていると考えられます。
しかし、カーフロスの問題やワイヤコストの問題があるのでインゴットがあまり安くならないのであれば、カーフロスが無く反りも小さいレーザスライシングが有利になってくると考えられているのです。
もし、レーザスライシングの装置価格及びランニングコストが下がってくれば、装置を2台3台と増設すること等により量産化に対応することも可能となるかもしれません。
参考文献
- 諏訪部仁:「シリコンと化合物半導体の超精密・微細加工プロセス技術 第2章 マルチワイヤソーによる半導体材料の切断加工」,株式会社シーエムシー出版,89,5, (2024.06), 19.
- 加藤智久:NEDOプロ「低炭素社会を実現する新材料パワー半導体プロジェクト」での大口径SICウェハ加工技術開発,精密工学会誌,80,1, (2014), 18.
- 糸数篤:「SiC,GaN加工技術セミナー資料 2日目『ウェハ切断』マルチワイヤ放電スライス技術」,日本工業出版株式会社, (2024.06.12)1.
- 山田洋平,池野順一:「SiCに対するレーザスライシングの実現可能性」,次世代固定砥粒加工プロセス専門委員会第118回研究会資料, (2024.12.06)21.