SiC半導体とは?基板加工技術について分かりやすく徹底解説
2024/10/24
2025/08/15
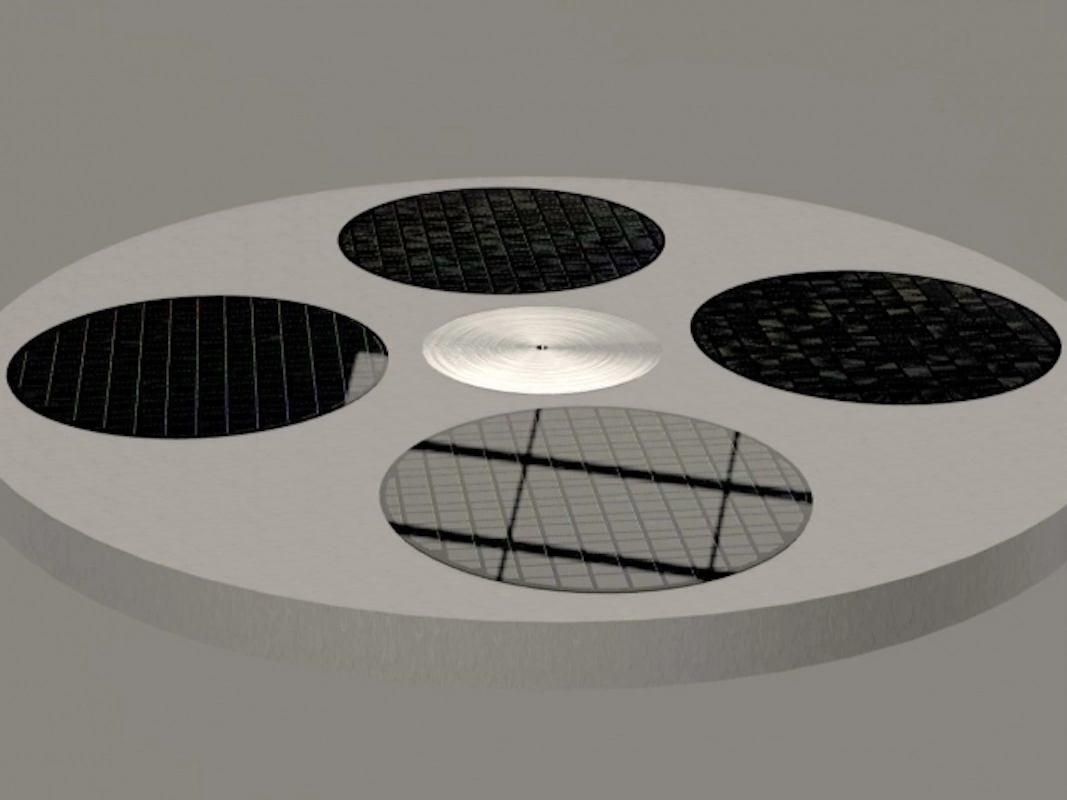
今回は、SiC半導体の基板加工技術について解説いたします。
SiC半導体(シリコンカーバイド半導体)とは、シリコン(Si)と炭素(C)で構成される化合物半導体材料のことを表しています。
SiC半導体の基板加工は応用編になりますので、加工の基礎編については「研磨加工とは?基本的な定義と種類・方法の基礎を徹底解説」の記事を参考にしてください。
最近注目を集めている「SiC半導体の基板加工技術」とはどのようなものかを詳しく解説していきます。
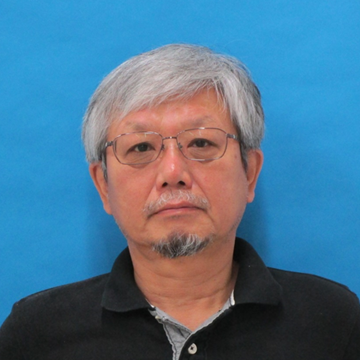
株式会社斉藤光学製作所技術顧問。専門が「研磨加工」と「微粒子分散」の技術コンサルタント。1976年、東北大学工学部を卒業後にタイホー工業株式会社 中央研究所にて磁性流体や研磨加工の研究に従事。1987年、東京大学より工学博士号(機械工学)を授与。2001年から3年間、東京大学生産技術研究所の客員教授。その後10年間は、研磨材メーカーの株式会社フジミインコーポレーテッド。さらにその後10年間は、国立研究開発法人 産業技術総合研究所 招聘研究員だった。
プロフィール詳細を見るSiC半導体とは何か?
私たちが日常で使うスマートフォンやコンピュータの心臓部には、半導体チップが使われています。
また、冷蔵庫、洗濯機、電子レンジなどの家電製品、自動車、医療機器などにも半導体は使われているのです。
さらに、半導体技術の進化は、人工知能(AI)やモノのインターネット(IoT)、量子コンピュータなどの新しい技術の発展を支えています。
このように、半導体は、私たちの生活のあらゆる面で中心的な役割を果たしており、その技術の進展は今後も私たちの生活を大きく変えていくことでしょう。
半導体デバイスの歴史
半導体デバイスの始まりは、1947年、アメリカのベル研究所で以下3人の科学者によって発明されたトランジスタになります。
・ジョン・バーディーン
・ウォルター・ブラッテン
・ウィリアム・ショックレー
この発明は、真空管に代わる新しい増幅素子として開発されます。
最初のトランジスタは「点接触型トランジスタ」と呼ばれ、ゲルマニウムの単結晶に2本の針を立てて電流を流すことで動作していました。
その後、1950年代に入ると、シリコン(Si)がトランジスタの基板材料として広く使われるようになり、現在ではシリコンが主流となっています。
半導体結晶の表面研磨の必要性は、1955年のゲルマニウム拡散型トランジスタの発明において重要性が認識されました1)。
平滑な表面は、電子がデバイス内をスムーズに移動できるようにし、デバイスの性能を向上させます。
最初の頃の研磨方法は微細なダイヤモンドスラリーや、アルミナによる機械的ポリシング法でした。
そして、ダメージフリー(無欠陥)の必要性から、主にコロイダルシリカを用いたCMP(Chemical Mechanical Polishing)法が使われ始めました。
そしてその後も、加工対象の広さや、使い勝手の良さ、材料の量産安定性やコストパフォーマンスの良さから広く普及しています。
半導体デバイスの種類とSiC半導体の用途
半導体デバイスは以下に大別されます。
- 演算を行うロジック半導体
- データを記憶するメモリ半導体
- 光、音、温度などの連続的なアナログ信号を処理・制御するためのアナログ半導体
- 高電圧や大電流を扱うパワー半導体
これらは通常、シリコン(Si)を基材とした半導体です。
このうち、ロジック、メモリ、アナログ半導体は、今後もシリコンが主要な材料として使われ続けると考えて差し支えないでしょう。
一方、パワー半導体の基材においては、シリコンは伝統的に最も広く使用されている材料であり、製造コストが低く技術的にも成熟しています。
しかし、高温や高電圧での性能には材質としての限界があるのです。
2050年のカーボンニュートラル社会の実現に向けては、より高性能な電力変換技術が必要とされており、シリコン半導体が持つ能力を大きく超える必要があるかもしれません。
こうした背景から、シリコンに代わる新しい半導体材料として、SiCやGaN、ダイヤモンドなどの先進パワー半導体が注目されています。
スイッチング性能とは

図1は、Siパワー半導体と先進パワー半導体であるSiCと、GaNのパワー半導体のスイッチング性能を比較したものです2)。
スイッチング性能とは、パワー半導体が扱えるon/offの能力を表します。スイッチング周波数は、1秒間当たりのパワー素子のon/off回数を示し、値が大きいほど高速に動作する性能に優れ、電力の制御性能が良い、という意味です。
スイッチング容量は、当該スイッチが扱える電圧と電流の積を示し、値が大きいほど大容量の電力を扱う性能に優れることを意味します。
この図では、図の右上の範囲ほどスイッチング性能が高いことを示しています。
現在のSiパワー半導体が対応可能な部分は、図中の左下に示される範囲です。
この範囲を右上方向に拡大し、Siのパワー半導体では対応が難しい性能を開拓する技術として、SiCやGaNのパワー半導体の開発が進められています。
SiC半導体の用途
その中でも、SiCは高温や高電圧での性能が優れています。
電力損失が少ないため、電気自動車や再生可能エネルギーの分野で注目されているのです。
SiCは高い電圧耐性、優れた熱伝導性、高速スイッチング能力などの特性を持ち、特に高電圧・高温環境での使用に適しています。
これにより、電力変換装置や電気自動車のインバータ、太陽光発電システムなどで広く利用されているのです。
炭化ケイ素(SiC)とは?
炭化ケイ素(Silicon Carbide)とは非酸化物セラミックスの一種で、炭素(C)とケイ素(Si)が1対1で結合したもので、化学式はSiCで表されます。
SiCは天然には存在せず、1891年アメリカでエドワードG.アチソンがダイヤモンドを合成しようとした際に、偶然発見したものといわれています。
今でも行われているアチソン法は炭素原料であるコークスなどや、ケイ素原料である硅石などを混合したものを電気炉(アチソン炉)に詰め、直接通電してインゴットを製造する方法です。
SiCの特徴
こうしてできたSiCは、次のような優れた特徴を持っています。
- 高い硬度
SiCの硬さは新モース硬度で表すと13で、ダイヤモンド(新モース硬度15)、炭化ホウ素(新モース硬度14)に次いで地球上で3番目に硬い化合物です。 - 熱的特性(熱伝導率、熱膨張率、耐熱性)
SiCは熱伝導率が高く(熱を伝えやすく) 、また、熱膨張率が低い(熱による体積変化がすくない)ため、熱衝撃には非常に高い耐性を持っています。
また、熱安定性が高く、大気圧下では溶融しません。分解(昇華)温度は約2545度で極めて優れた耐熱性を有しています。 - 耐酸化性・耐食性
SiCは粒状の場合、700℃以上で酸化が始まるといわれており、その酸化物(SiO2)がSiCの表面を覆い、酸化に対し保護膜となるため、酸化が抑制されます。
また、極めて安定した化合物で、酸やアルカリにも侵されにくく、非常に優れた耐薬品性を有しています。 - 電気的性質
SiCは半導体の性質を有し、電気抵抗が発熱体として使用できる低抵抗領域から絶縁体に近い領域まで変化します。
以上のように、SiCは有益な特性を数多く持っており、その特性を生かして耐火材や研磨材・研削材として利用されてきました。
近年はファインセラミックスやエンジニアリングセラミックス、半導体の材料としても注目されてきています。
昇華法 | ガス法 | 溶液法 | |
成長原理 | ![]() | ![]() | ![]() |
特徴 | ・最も実施されている量産手法 | ・原料を連続的に供給 ・高純度原料 ・成分組織制御に優れる | ・Si、GaAs引上法に類似 ・大口径、長尺 ・高品質化の可能性あり |
課題 | ・口径拡大 ・長尺化 ・品質を維持した高速化 | ・ガス流れ/温度分布制御 ・ガス導入、排出部詰まり | Si溶液中での ・炭素溶解度の向上 ・金属混入 |
SiC単結晶の製法と特徴
半導体の材料として使用されるのは、単結晶のSiCです。
SiC単結晶の製法には、表1に示すようないくつかの方法がありますが、代表的なものとしては「昇華法」があります。
SiC単結晶の製法の代表「昇華法」とは?
昇華法は、SiCの原料を高温で昇華させ、その蒸気を種結晶上に再結晶させる方法で、昇華したSiCが不活性ガス中を拡散し、種結晶上で凝結する手法になります。
メリットとしては、高品質な大口径単結晶を得られます。
現在市販されているSiC単結晶基板のほとんどがこの方法で製造されており、現在は6インチから8インチへの大口径化が進んでいるのです。
こうして製造されたSiC単結晶は、シリコン単結晶と比較すると、表2に示すような特徴があります。
Si | SiC | SiCの特徴 | 効果 | |
エネルギーバンドギャップ(eV) | 1.12 | 3.26 | 高温、高電圧でも動作 | ・高温動作 ・高耐圧、大容量 |
絶縁破壊電界(MV/cm) | 0.3 | 3.0 | 厚みを1/10にできる オン抵抗2~3桁小さい | ・高パワー密度(小型化) ・低損失 |
熱伝導度(W/cm・K) | 1.5 | 4.9 | 機器の冷却簡易化 | ・小型化 |
- 高い絶縁破壊電界強度:SiCはシリコンの約10倍の絶縁破壊電界強度を持ち、高電圧に耐えられます。
- 広いバンドギャップ:SiCのバンドギャップはシリコンの約3倍で、高温環境でも動作可能です。
- 高い熱伝導率:SiCは熱を効率的に伝えるため、デバイスの冷却が容易です。
- 高い移動度:電子の移動度が高く、高速なスイッチングが可能です。
これらの特性により、SiCは電気自動車や再生可能エネルギーシステムなど、効率的な電力変換が求められる分野で広く利用されています。
現状はSiCウエハの需要が拡大
では次に、SiC基板加工の現状と、加工の際にどのような課題があるかを詳しく解説いたします。
近年、地球温暖化による異常気象が大きな社会問題となっており、気候変動の影響を最小限に抑えるための取り組みとして、カーボンニュートラル社会の実現が要望されています。
カーボンニュートラル社会とは、温室効果ガスの排出量をゼロにすることを目指す社会のことです。
これは、地球温暖化を防ぎ、気候変動の影響を最小限に抑えるための取り組みになります。
カーボンニュートラル社会の実現には、再生可能エネルギーの利用拡大や、エネルギー効率の向上、EVなどモビリティーの電動化などが必要です。
そのため、SiCやGaNなどの先進パワー半導体による新しいパワーエレクトロニクス技術が不可欠となっています。
特にEVには大量のSiCパワーデバイスが必要とされ、SiCウエハの量産化・低コスト化が強く望まれているのです。
ウエハサイズにおいても、現在は6インチが主流ですが、世界の主要なウエハメーカーでは、次々と8インチウエハの製造工場が稼働し始めるなどウエハの大口径化や市場規模の拡大は確実に進んでいます。
しかし、同時にSiCは研磨材としても使用されるほど極めて高硬度かつ化学的・熱的にも安定な材料です。
現状では、インゴット切断から最終研磨まで加工には多くの時間とコストがかかっています。
そのため、ウエハの大口径化・量産化に向けて加工技術の大幅な改善が求められています4)。
Siウエハの加工プロセス
現在、半導体結晶材料の代表であるSi(シリコン)は、12インチ換算で年間1億枚ものウエハが生産されています。
一工場当たり月産数十万枚ものウエハが生産されており、その加工プロセスは数十年に渡り変革を重ねて現在に至っているのです。
基板加工プロセスにおいても安定した大量生産のため、いくつもの工程が効率良く組み込まれています。
このことはSiCにおいても大いに参考にされるべきと考えられるでしょう。
代表的なSiウエハ加工プロセスの概要を以下に示します。
1.インゴットの製造
純度の高いシリコンを原材料として使用し、高温で溶かしてシリコンインゴットを作成。
これには、チョクラルスキー法やフロートゾーン法といった方法が用いられます。
2.インゴットの成形と切断
まず、冷却したシリコンインゴットを外形研削により円柱形に成形し、円形のシリコンウエハに切断。
次に、マルチワイヤソーを使用して薄くスライスする方法です。
研磨材としては、炭化ケイ素粉末をオイルに分散させたスラリーやワイヤーに、ダイヤモンド粉末を固定させた固定砥粒が用いられます。
3.べべリング、ラッピング
次にウエハの端面をダイヤモンド砥石でべべリング(面取り)し、その後のラッピング工程において、切断時にできた表面の凹凸を除去しながら厚みを揃え、ウエハを所要の平坦度に加工。
この加工においては、アルミナとジルコンサンドによる複合人造エメリー(FOなど)を水溶液中に分散させたスラリーが用いられます。
多くの場合、両面同時ラッピングが行われます。
4.エッチング、ポリシング(CMP)
ラッピングされたウエハは、酸やアルカリによる常温のウェットエッチングによって加工変質層が除去された後、エッジポリッシュ工程にてウエハ端部を加工。
その後、ポリシング(CMP)工程にてウエハ表面を鏡面に仕上げます。
ポリシングは、一次ポリシング、二次ポリシング、ファイナルポリシングと多段で加工。
研磨材には一次/二次ポリシングでは、砥粒としてアルカリで調整したコロイダルシリカまたは微粒子ケイ酸が主として用いられます。
ファイナルポリシングでは、半導体に悪影響を与える金属不純物をほぼゼロに抑えた高純度コロイダルシリカが用いられます。
SiC基板加工の課題
SiC基板加工にはいくつかの課題があります。
その中でも、代表的な課題を2つ紹介します。
課題1:SiとSiCの加工プロセスの違い
後発となるSiCの加工プロセスにおいてもSiに習うのが常道と考えられます。
しかし、表3に示すように,材料の特性において両者には大きな違いが二つあります。
一つは、材料の硬度の違いです。
Siはモース硬度7(ヌープ硬度560~710)であり、それほど硬くはないため、GC(SiC)系砥粒やWA系砥粒のような一般砥粒で、比較的安価に切断や機械的加工ができます。
それに対してSiCはモース硬度13(ヌープ硬度2400~3000)と非常に硬いため、機械的に加工するためには最も硬くて高価なダイヤモンド砥粒を使う必要があるのです。
SiC | Si | |
---|---|---|
修正モース硬度 | 13 | 7 |
ヌープ硬度 | 2,400〜3,000 | 560〜710 |
融点 | ー | 1,410°C |
昇華点 | 2,000〜2,200°C | ー |
薬品融解性 | 溶融アルカリ(600°C前後) | アルカリ(常温) |
もう一つは、材料の安定性です。
Siは薬品に対して比較的弱い性質があるため、ラッピング後の酸やアルカリによる常温ウェットエッチングによりダメージ層を完全に除去でき、その後のCMPへの負担は抑制できます。
一方、SiCは熱的にも化学的にも極めて安定であるため、いかなる薬品を用いても常温ウェットエッチングは不可能です。
そのため、SiCにおいては研削かダイヤモンドラッピングで砥粒の粒度を変えて、徐々にダメージ層を小さくしてからCMPで仕上げなければなりません。
図2は、SiCの基板加工プロセスの概要を示します。
スライシング・べべリング後の粗加工から中間加工(CMPの前加工)工程を研削で行うか、ラッピングで行うか、現時点では確立されていないことがポイントです。

課題2:SiとSiCの実加工時間
以上のように、SiCは切って磨くだけでも時間とコストがかかるため、早くからウエハ加工の高速化・低コスト化が叫ばれていました。
そこで、2010年から5年間行われた国家プロジェクト「低炭素社会を実現する新材料パワー半導体プロジェクト」 (通称「FUPET」)において、『大口径ウエハの高速加工技術開発』が課題に取り上げられます。
当初は50時間以上かかると見込まれた6インチウエハの「切断からCMPまでの一貫加工時間」を、プロジェクト終了時には10時間以内に収められました5)。
そのときの粗加工および中間加工のメインは高剛性研削機を用いた片面のロータリー研削方式でした。
SiCは極めて高硬度であるために砥粒を高荷重で押し込む必要があります。
そこで、ウエハ裏面を吸着して片面ずつ加工する片面研削方式が有利であり先行しました。

図3は、6インチウエハ1枚当たりの実加工時間をSiCとSiとで比較したものです。
元となっているデータ(表4)は筆者の独自調査の結果ではありますが、SiCはSiの5倍程度加工時間が長いことが分かります。
Siに比べて明らかに時間がかかっている工程が切断とCMPです。
したがって、この二つの工程は画期的な改善が必要になります。
また、SiCの加工プロセスではダイヤモンド砥粒が主に使用されていますが、砥粒と工作物の硬度が近いため、砥粒減耗速度(擦り減り方)も大きいと思われているのです。
そのため、加工コストとしては5倍ではとても済まないであろうと思われます。
そこが現状における最大の課題と言えるでしょう4)。
SiCウエハ | 実加工時間 | 同時加工枚数 | 1枚当たりの時間 |
---|---|---|---|
切断(ダイヤ固定ワイヤ) | 9時間 | 30枚 | 18分 |
粗研削(ダイヤホイール) | 3〜5分(片面) | 1枚 | 6~10分 |
精研削(ダイヤホイール) | 3〜5分(片面) | 1枚 | 6~10分 |
高速CMP | 60分 | 5〜8枚 | 7.5~12分 |
高品質CMP | 20分 | 5〜8枚 | 2.5~4分 |
合計 | 10時間26分~10時間30分 | 40~54分 |
Siウエハ | 実加工時間 | 同時加工枚数 | 同時加工枚数 |
---|---|---|---|
切断(GC) | 4~5時間 | 300枚 | 0.8~1分 |
両面ラップ(FO) | 20分 | 20枚 | 1分 |
ディップエッチング | 数分~数十分 | 25枚 | 0.2~2分 |
1次ポリシング | 20分程度 | 5~8枚 | 2.5~4分 |
2次ポリシング | 10分程度 | 5~8枚 | 1.25~2分 |
ファイナルポリシング | 10分程度 | 5~8枚 | 1.25~2分 |
合計 | 5時間10分~7時間 | 7分~12分 |
表4.SiCおよびSiの工程別加工時間( 6インチウエハの場合)
SiC基板加工の現状と課題まとめ
現状のウエハ加工プロセスの課題について総論的に述べました。
今後は、各論として、切断からCMPまでの各工程を具体的に順次解説していく予定です。
次回は「SiCインゴットの切断技術」について解説します。
その他、以下について取り上げる予定です。
- SiCの研削研磨技術やCMP技術
- SiCウエハの評価技術
- 潜傷
- デバイス信頼性
- 酸化援用加工
それでは、次回をお楽しみに。
参考文献
1) I. Koshiyama:Research and Development on the Processing Methods of Substrate Surfaces for Electronics and the Consumable Materials, Doctoral Dissertation of I. Koshiyama, Japan (2006).
2)国立研究開発法人 産業技術総合研究所:ワイドバンドギャップ半導体によるパワーエレクトロニクス技術のスペックロードマップ,June(2023).
3)加藤智久,「SiCバルク単結晶とその革新的切断技術の開発」,次世代固定砥粒加工プロセス専門委員会 第61回研究会(2015.6)
4)河田研治:「パワーデバイス用SiCウエハ加工の現状と展望」,精密工学会誌,89,5,(2023), 359.
5)加藤智久:NEDOプロ「低炭素社会を実現する新材料パワー半導体プロジェクト」での大口径SICウェハ加工技術開発,精密工学会誌,80,1,(2014), 18.