ポリシングに用いられる「砥粒」とは?種類と特徴を徹底解説!
2024/07/30
2025/08/15
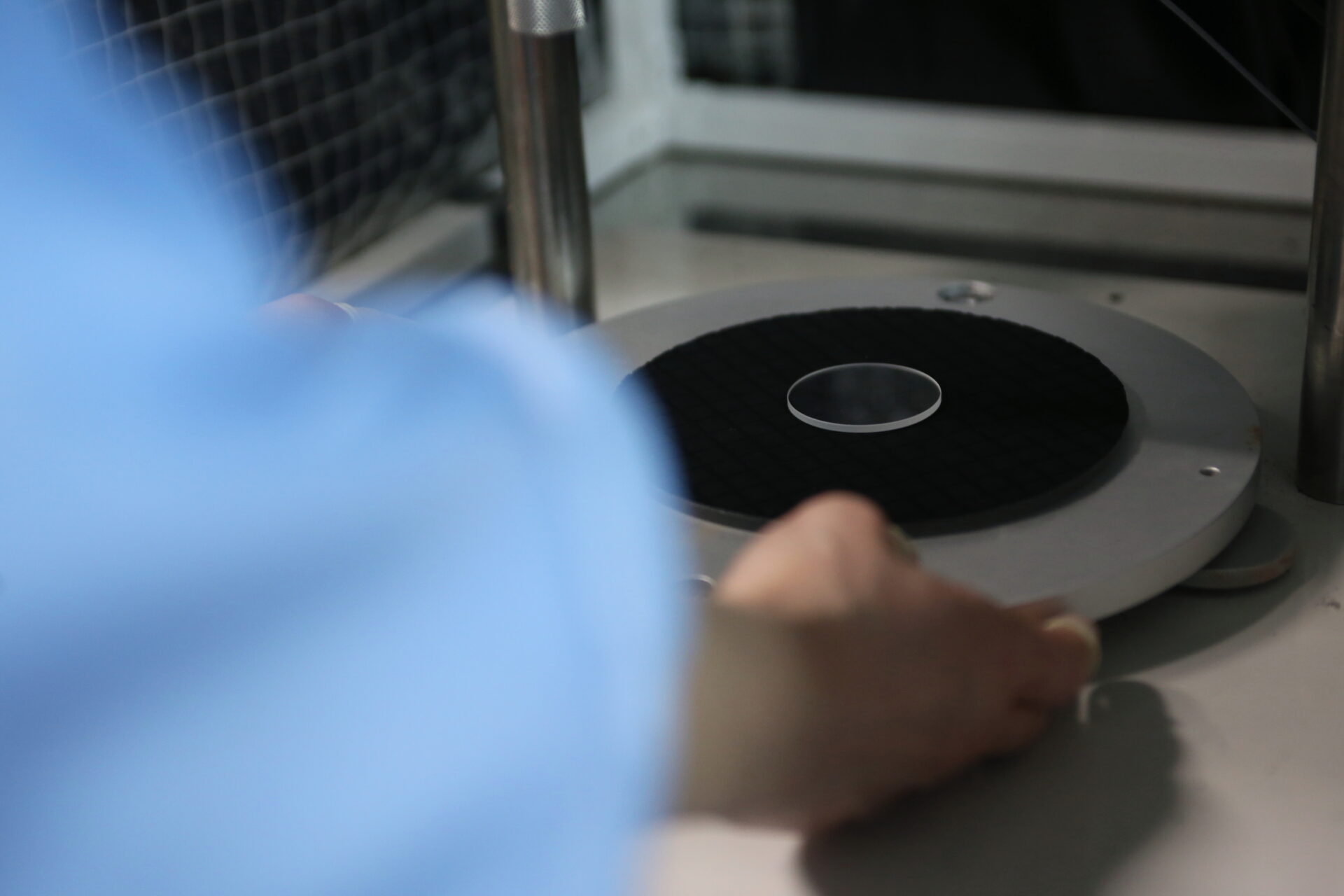
前回の記事でラッピングの砥粒について解説いたしましたが、今回はポリシングにおける砥粒についてのお話になります。
ポリシングにおける砥粒の位置付けから、ポリシングスラリーの構成成分、種類と特徴について詳しく解説していきます。
まずはポリシングに用いられる砥粒の位置付けからお話ししましょう。
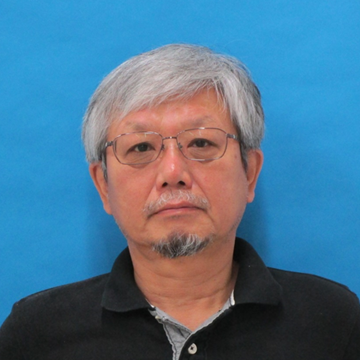
株式会社斉藤光学製作所技術顧問。専門が「研磨加工」と「微粒子分散」の技術コンサルタント。1976年、東北大学工学部を卒業後にタイホー工業株式会社 中央研究所にて磁性流体や研磨加工の研究に従事。1987年、東京大学より工学博士号(機械工学)を授与。2001年から3年間、東京大学生産技術研究所の客員教授。その後10年間は、研磨材メーカーの株式会社フジミインコーポレーテッド。さらにその後10年間は、国立研究開発法人 産業技術総合研究所 招聘研究員だった。
プロフィール詳細を見る1.ポリシングにおける「砥粒」の位置付け
では「ポリシングに用いられる砥粒」について詳しく解説します。
ラッピングとポリシングは、最も広く一般的に実施されている研磨法です。
歴史的にも一万年もの昔から石斧や石皿などの磨製石器や、装飾用の勾玉や管玉、儀式に使う水晶玉などがハンドラッピングやハンドポリシングの類で磨かれていました。
その後、ルネッサンス以降の天体望遠鏡の発達とともに光学レンズの精密仕上法として発達し、現在では、半導体をはじめとした電子材料、光学材料などの最終仕上げ工程として広く用いられています。
ラッピング | ポリシング | |
位置付け | 粗加工 ポリシング前の加工 | 仕上げ加工 |
目的 | 目的の寸法、形状を得る | 鏡面仕上げ、ダメージ除去 |
取り代・砥粒径・砥粒硬度 | 大 | 小 |
砥粒の作用機構 | 機械的作用が主 | 科学的作用との併用 |
表1には、ラッピングとポリシングの目的や使用する砥粒の違いを比較して示しています。
ラッピングとポリシングの間に厳密な仕切りというものはありません。
ラッピングは目的の寸法や形状を得るための粗加工、ポリシングは工作物表面を鏡面にしたり、工作物内部に残存しているダメージを除去するための仕上げ加工と位置付けられています。
また、時にはラッピングはポリシングの前加工という位置付けです。
このため、ラッピングには比較的粗くて硬い砥粒が使用され、ポリシングには比較的細かく軟らかい砥粒が使用されます。
また、ラッピングが主として砥粒の機械的作用によって行われるのに対し、ポリシングは機械的作用のほかに、砥粒自身と工作物、あるいは研磨液と工作物との化学的作用が大きく影響しているのです。
2.ポリシングスラリーの構成成分
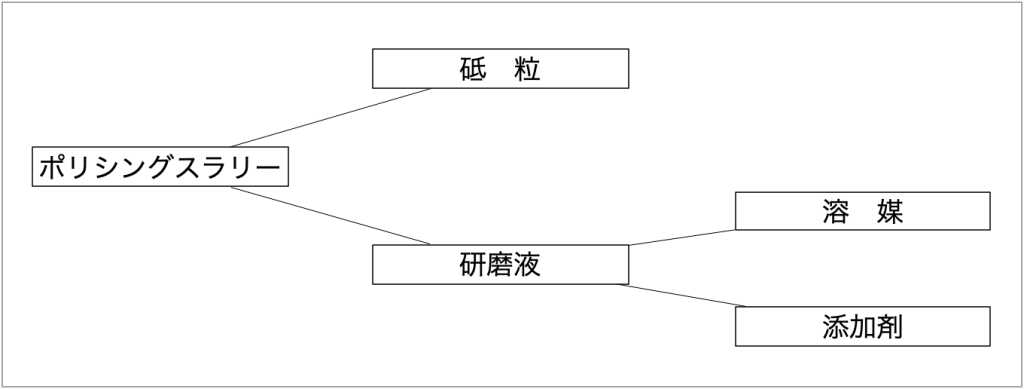
ポリシングは、乾式で行われる場合も全くないわけではありませんが、大体は湿式で行われ、溶媒に砥粒を分散したスラリーを使用して行われます。
また、ラッピング用砥粒はほとんどが粉体状研磨材として販売されるのに対し、ポリシング用砥粒は水に分散した状態で添加剤も加えたスラリー状研磨材として販売されることが少なくありません。
ポリシングスラリーは、図1に示すように、砥粒と研磨液から成り、研磨液は溶媒と各種の添加剤で構成されます。
特殊な例として、砥粒なしで、研磨液の化学的作用のみで研磨(ケミカルポリシング)する場合もあるのです。
研磨液の主成分である溶媒は、ほとんどの場合において「水」です。
但し、水に溶けてしまう工作物の場合などは水以外の溶媒(油など)を使用することもあります。
水の役割としては、「砥粒の分散媒としての役割」「切り屑の排出」「冷却」「洗浄作用」などです。
添加剤は、砥粒と溶媒のみでは要求される研磨性能が達成できない場合に配合される薬剤です。
加工促進、面精度向上、面性状良化、分散性向上などの目的で、酸やアルカリ、酸化剤、錯化剤、界面活性剤、水溶性高分子、防錆剤、消泡剤、防カビ剤などが添加されます。
3.ポリシング用砥粒の変遷
元来、ポリシングは仕上げ加工として行われるため、天然の砥粒の中でも、傷がつかないように、水簸などで細かい砥粒のみを選別して使用されてきました。
天然砥粒としては地球上に豊富に存在するシリカ質のものが主体で、比較的研削能力の高いガーネットやエメリーなどの砥粒は貴重な資源でした。
これらの鉱物の主成分がアルミナ質であったことから人造のアルミナ砥粒が製造され実用化されたのはほぼ20世紀に入ってからで、それほど古い話ではありません。
また、天然ダイヤモンドやコランダム(ルビー、サファイアなど)の飛びぬけた研削力はその宝石としての魅力と相まって人造化への懸命な努力が続けられていたのです1)。
今から約60年ほど前の1960年ころまでは高精度ポリシングの対象はガラスレンズや金型、精密金属部品などであり、砥粒には小さくてもサブミクロン級のアルミナやセリアなどが主に使われていました。
ところが、その後半導体トランジスタが発明され、ゲルマニウムやシリコンなどの半導体材料にターゲットが移ります。
ポリシングにおいてもダメージフリー(無欠陥)の必要性からコロイダルシリカが使われ始め、その後も加工対象の広さや、使い勝手の良さ、材料の量産安定性やコストパフォーマンスの良さから広く普及してきました。
現在、半導体トランジスタはムーアの法則に従って高集積化が進み、デザインルールの微細化に伴って、仕上面粗さ(Ra)は原子レベルの平坦性・平滑性が求められています。
それに対し、主にコロイダルシリカを用いたCMP(Chemical Mechanical Polishing)技術の発達により1ÅオーダーのRaが実現されました。
4.ポリシング用砥粒の種類と特徴
現在、ポリシングに使用される主な砥粒種は、シリカ系砥粒、アルミナ系砥粒、セリア、ジルコニア、ダイヤモンドです。
このうち、アルミナ系砥粒とダイヤモンドはラッピング用砥粒として解説済みですので、以下では、それ以外の各砥粒の特徴や用途、製法などについて解説します。
4-1.シリカ系砥粒
ポリシングに使用されるシリカ系砥粒を大別すると、パウダー状シリカ(シリカゲル)を研磨液に分散したものと、コロイダルシリカのように元々分散媒中で製造されたもの(シリカゾル)があります。
シリカゲルには、乾式法無水ケイ酸(フュームドシリカ)と湿式法含水ケイ酸(沈降法シリカ)があり、シリカゾルには、解膠法コロイダルシリカや、イオン交換法コロイダルシリカ、超高純度コロイダルシリカがあります。
代表的な用途は、なんといってもシリコンです。
シリコンウェハの研磨材として、開発当初は米国でサブミクロン級のジルコニアが加工能率の点から使用されましたが、表面のマイクロスクラッチや潜傷(表面下に潜む加工歪)の問題からシリカ系砥粒が選ばれました。
沈降法シリカやフュームドシリカも検討されましたが、最終的にはその頃量産化が進んできていたイオン交換法によるコロイダルシリカが残ったと言われています。
それに加工促進剤として無機アルカリや有機アミンを添加したCMPスラリーが現在でも主流です。
イオン交換法 (通常コロイダルシリカ) | 水ガラス(ケイ酸Na)溶液をイオン交換樹脂に通してNaイオンを除くとシリカが析出。大量生産により低コスト。純度は低い | ![]() |
煙霧法、熱酸化法(フュームドシリカ) | 四塩化ケイ素を高熱で水と反応させて生成した微粉末シリカを水に分散。高純度。分散性は悪い | ![]() |
ゾルゲル法(超高純度コロイダルシリカ) | ケイ素アルコキシドをアルコール中で加水分解するとシリカゾルが生成される。超高純度 | ![]() |
表2にはシリコンウェハ製造に用いられるシリカ系砥粒の製法と特徴を示します。
シリコンウェハ製造におけるポリシングは、能率重視の一次ポリシング、形状・粗さ重視の二次ポリシング、最終仕上げとなるファイナルポリシングがあります。
表面に何もついていないベアシリコンには金属イオンが拡散しやすくなっています。
そのため、無歪無汚染が要求されるファイナルポリシングでは汚染物質となる金属原子を含まない超高純度コロイダルシリカが使用されます。同様に、デバイスシリコンのプラナリゼーションCMPにも超高純度コロイダルシリカが使われます。
超高純度シリカ | フュームドシリカ | イオン交換法シリカ | |
Fe | ND | 133 | 23,200 |
Al | ND | 430 | 179,800 |
Ca | ND | 114 | 7,000 |
Ti | ND | 520 | 25,800 |
Ni | ND | ND | 72 |
Cu | ND | ND | 212 |
表3には、各シリカ系砥粒に含まれる金属不純物イオンの濃度を示します。
イオン交換法コロイダルシリカ>> フュームドシリカ > 超高純度コロイダルシリカの順で不純物が少ないことが分かります。
ND(Not Detectedの略)とは、検出できないほど少ない(ほとんどゼロ)という意味です。
4-2.セリア
セリア(酸化セリウム)はガラスのポリシングに良く使用されています。
元々、日本ではガラスの仕上げ研磨にはベンガラ(α-酸化鉄)が使われていましたが、1960年頃から米国製セリアを起点として国内でもセリアが導入され、その研磨能力の高さから市場に急激に広まりました。
当時は板ガラスの研磨が主体でしたが、その後は光学レンズや液晶表示装置、フォトマスクなどの仕上げ研磨に大量に使用されました。
2010年頃に希土類元素の高騰でセリアも10倍近くの価格に上昇し、一時大騒ぎになりました。
しかし、使用する各社が工程を工夫して使用量を減少したり代替砥粒を開発したりして凌いでいるうちに価格も治まり、現在は、半導体、電子工業、光学工業などの分野で液晶ガラス基板、光学レンズ、ハードディスク基板などに広く使われています。
セリアは、出発原料により、塩化希土系とバストネサイト系に分けられ、更に酸化セリウムの品位により高セリウム研磨剤と低セリウム研磨材とに分けられます。
セリア砥粒の研磨力は焼成温度に影響され、それぞれに研磨力が最高になる温度範囲があるのです。
例えば、バストネサイト系では850~950℃でじっくり焼成されたものが良いと言われています。
セリアは元々数種類の希土類元素を含有した鉱物資源ですが、EVモーターの磁石などに使用する高付加価値の元素を取り除くことで薄いベージュ色、乃至、白色のセリアができるのです。
最近は、セリアの安定供給を目的として、白色系のセリアや、他元素を徹底的に除去した高純度セリアが供給されてきています。
高純度セリアは、セリウム含有鉱石(例えば、モナズ石やバストネサイト)からセリウムだけを抽出して酸化させることで得ることができ、高純度を保つために、精製プロセスで不純物を徹底的に除去します。
一般的な製造方法には、化学沈殿法、溶液燃焼法、ソルボサーマル法などがあります。
4-3.ジルコニア
ジルコニアは、前述のように、米国においてシリコンウェハ用ポリシング剤として使用されたこともありますが、面品質がコロイダルシリカには適わなかったことから淘汰されました。
しかし、チタニウム、ニッケル、モリブデンなどの特殊合金の研磨や、光学レンズの最終研磨には適しており、依然として一定の需要はあるようです。
ジルコニア砥粒は、酸化ジルコニウム(ZrO₂)を主成分とする砥粒で、優れた機械的特性を持ち、研磨や切削の用途に広く使用されています。
モース硬度は8.5~9に相当し、硬度が高いだけでなく、靭性も優れています。
高温環境でも安定しており、耐熱性にも優れています。溶融点は約2,700℃です。
天然にはジルカイトやバデライトとして産出しますが、工業的にはジルコンサンド(ZrO2・SiO2)を原料として、アーク溶融法や高温NaOH溶融法、塩素化後の焼成などによって合成されます。
参考文献
- 岡田昭次郎:砥粒・砥石よもやまばなし、砥粒加工学会誌,Vol.39,№2,(1995)26.