ポリシング加工の原理とは?研磨加工のメカニズムについて徹底解説
2024/03/28
2024/06/25
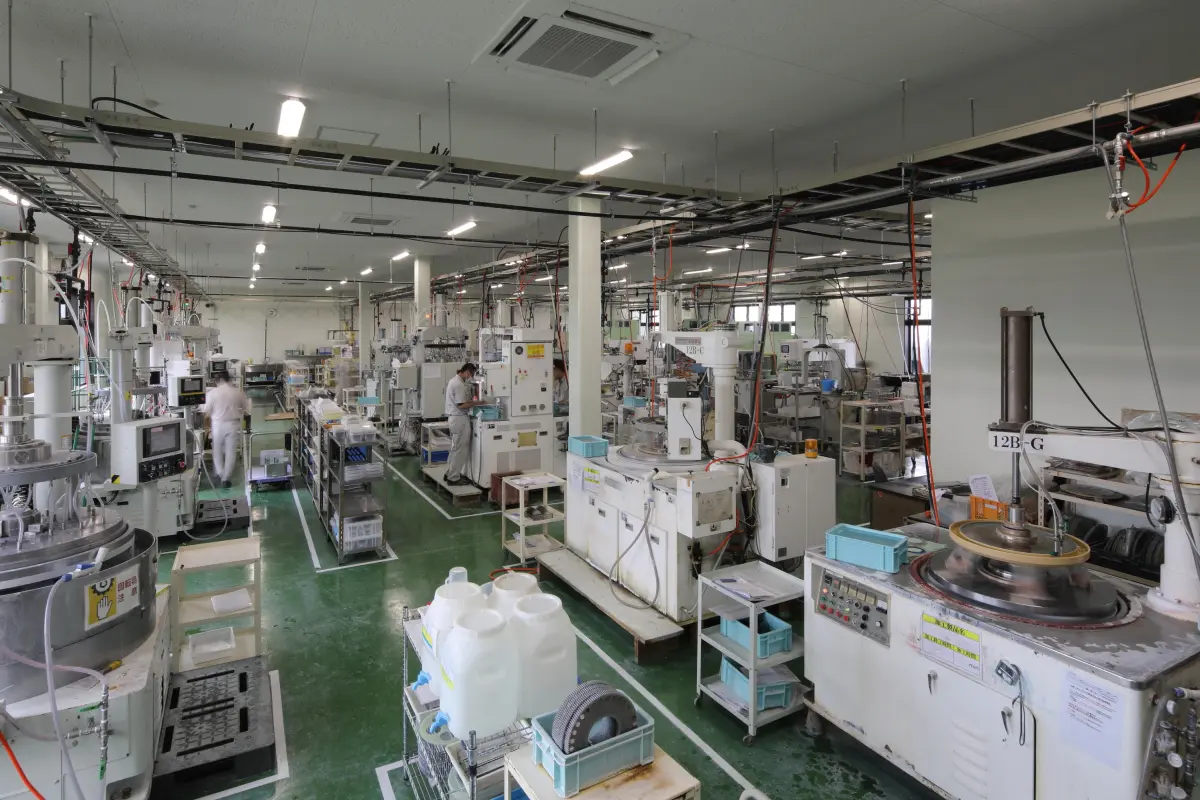
今回はポリシング加工に着目して、研磨加工のメカニズムについて解説していきます。
ポリシング加工と付随してよく見られるのはラッピング加工です。
それぞれ具体的にどのような違いがあるのか、またポリシング加工の中でも以下の詳細について見ていきます。
- 機械的ポリシング
- メカノケミカルポリシング
- ケモメカニカルポリシング
- ケミカル-メカニカルポリシング
- その他の新しいポリシング法
- 磁気的エネルギー援用研磨法
- 電気的エネルギー援用研磨法
それでは、一つずつ詳細を見ていきましょう。
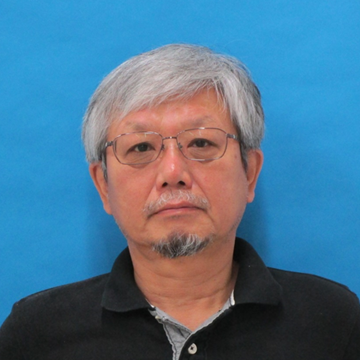
株式会社斉藤光学製作所技術顧問。専門が「研磨加工」と「微粒子分散」の技術コンサルタント。1976年、東北大学工学部を卒業後にタイホー工業株式会社 中央研究所にて磁性流体や研磨加工の研究に従事。1987年、東京大学より工学博士号(機械工学)を授与。2001年から3年間、東京大学生産技術研究所の客員教授。その後10年間は、研磨材メーカーの株式会社フジミインコーポレーテッド。さらにその後10年間は、国立研究開発法人 産業技術総合研究所 招聘研究員だった。
ポリシング加工とは?ラッピングとの違い
ラッピングの役割は粗加工であり、比較的粗くて、工作物より硬い砥粒を用いるため、砥粒の機械的作用が主でした。
それに対し、ポリシングは仕上げ加工であるため、比較的微細で軟質の砥粒と軟質な工具が用いられます。
また、工作物と化学的に反応する砥粒や研磨液が選択されることもあります。
それは、以下2つが原因となり、現在では化学的作用を併用したものが主流です。
- 機械的作用だけでは能率が低いこと
- 半導体材料の仕上げ加工においては、加工ダメージのない完全無歪な面が求められること
ポリシング法を加工メカニズムで分類すると、表1の5つに分別できます。
尚、化学的作用を併用したポリシング法の呼称は研究者によって違いがあります。
ここでは、公益財団法人 精密工学会の調査研究分科会における整理法注1)に準拠したものです。
分類 | 原理 | 事例 | |
---|---|---|---|
1 | 機械的ポリシング Mechanical Polishing(MP) | 微細砥粒による(塑性変形を主体とした)微小切削作用により鏡面化する。あるいは、摩擦熱により接触点局部を軟化させ、塑性流動により平滑化する | 具体例として微細アルミナによるアルミニウムディスクの研磨。微細ダイヤによるセラミックス、SiC、GaN単結晶のメカニカルポリシング(MP) |
2 | メカノケミカルポリシング Mechanochemical Polishing(MCP) | 工作物と、それより軟質な砥粒との固相反応を利用した方法で、砥粒と加工物とが接触する極微小領域での高温高圧により生じる反応物を砥粒でかきとる | コロイダルシリカによるサファイヤの仕上げ研磨が有名。微小領域でムライトが生成され除去される |
3 | ケモメカニカルポリシング Chemomechanical Polishing | 研磨液と工作物との化学反応(水和、酸化)を砥粒の擦過作用により励起させ、できた反応生成物を砥粒でかきとる | セリアによるガラスの研磨、SiC単結晶の酸化剤援用研磨など |
4 | ケミカル‐メカニカルポリシング Chemical-Mechanical Polishing(CMP) | 研磨液の化学的エッチング作用と砥粒の機械的切削作用とを複合させたプロセス | シリコンウェハの最終仕上げ(一次、二次、ファイナルポリシング)に採用されている |
5 | その他の新しいポリシング法 | 機械的エネルギー以外の磁気や電気エネルギーを付加して行う方法、工具と加工物が直接接触しないようにして歪の小さい加工を行う方法など | 磁気援用研磨、電気援用研磨、非接触研磨など |
注1)
- ケミカル・メカニカルポリシング:砥粒による力学的微小切削作用と、加工液(あるいは雰囲気気体)の化学的溶去作用との複合効果で除去する方法。
- ケモメカニカルポリシング:雰囲気の作用によってワーク表面に生じた反応生成物(酸化膜や水和膜など)を、砥粒の微小切削作用で除去する方法。
- メカノケミカルポリシング:砥粒との接触で生ずる機械的応力により、接触点近傍に誘起される反応生成物を、砥粒に付着させて除去する方法。
機械的ポリシング
機械的ポリシング(Mechanical Polishing:MP)の加工の模式図を図1に示します。
基本原理は、微細砥粒による、(塑性変形を主体とした)微小切削作用です。
それにより材料が除去され鏡面化されます。
また、金属材料においては、摩擦熱により接触点局部が軟化し、塑性流動による平滑化も起こります。
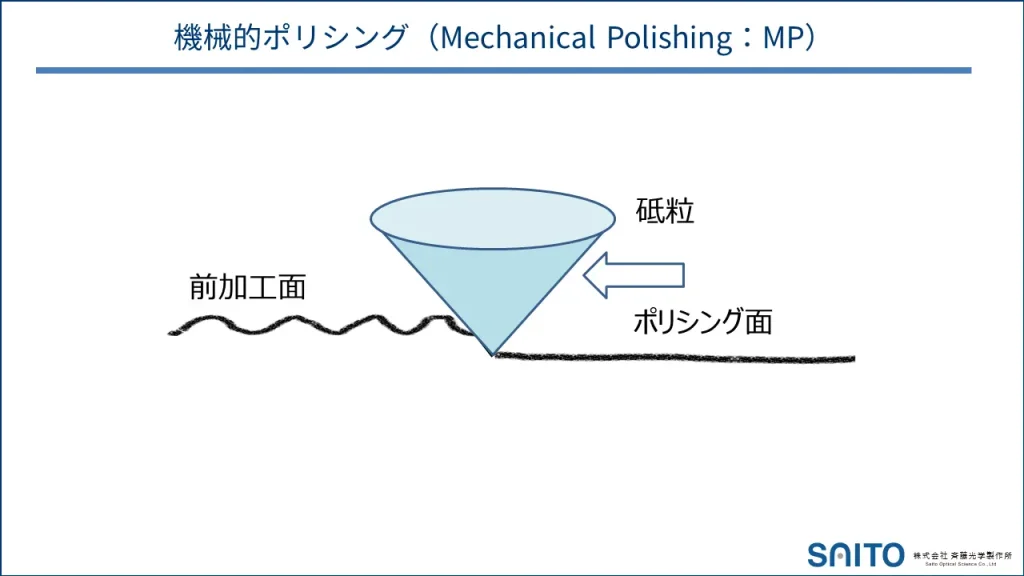
事例として、古くは勾玉や金属鏡の研磨がこれに該当すると言われています。
現在でも、金属やセラミックスなどの精密部品の仕上げに多用されています。
具体例としては、以下の3つです。
- 微細アルミナによるアルミニウムディスクの研磨
- 微細ダイヤモンド砥粒によるセラミックス類やSiC
- GaNなどの単結晶材料のメカニカルポリシング(MP)
市販のSiC単結晶ウェハにおいては、 非デバイス面であるC面がダイヤスラリーと研磨布によるMP仕上げであることが多いです。
メカノケミカルポリシング
メカノケミカルポリシング(Mechanochemical Polishing:MCP)の基本原理は、工作物と、それより軟質な砥粒との固相反応を利用した方法です。
砥粒と工作物とが接触する極微小領域において、高温高圧により生じる反応物を砥粒でかきとることにより研磨が進行します(図2)。
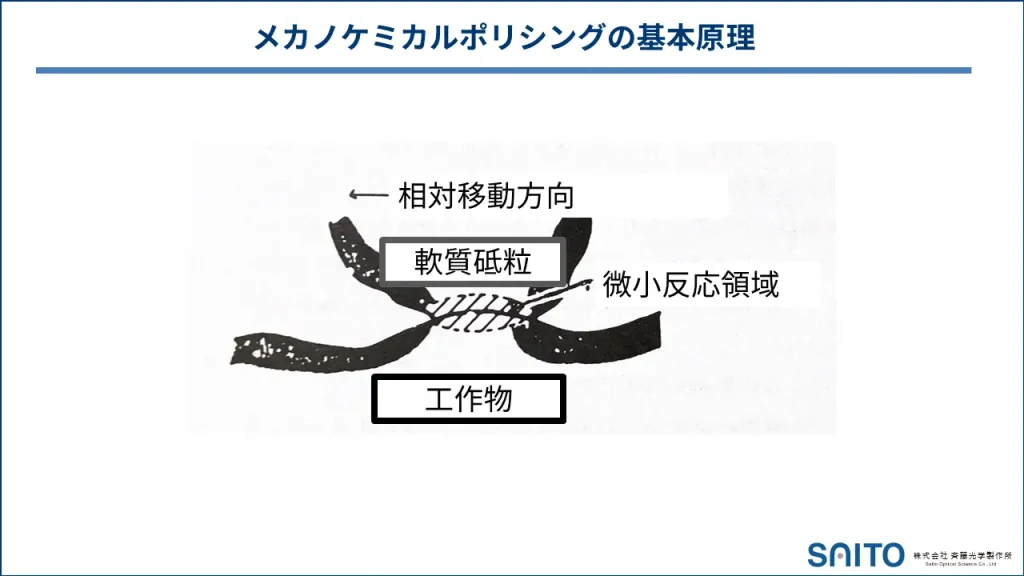
図2.メカノケミカルポリシングの基本原理2)4)
代表的な事例としては、コロイダルシリカによるサファイアの仕上げ研磨が有名です。
シリカ砥粒とサファイア表面が擦れ合う微小領域でムライトが生成され除去されます(図3)。

このメカノケミカルポリシングの基本原理は、現在、砥粒加工学会の次世代固定砥粒加工プロセス専門委員会顧問の安永暢男先生によって、サファイアの摩擦界面における化学現象をもとに着想されたものです。
安永先生は、1965年に通産省工業技術院傘下の電気試験所(現国立研究開発法人 産業技術総合研究所)田無分室の材料加工研究室に配属となり、最初に与えられた研究テーマが「アルミナ砥石の摩耗機構の解明」であったそうです1)。
当時、戦後の国際協力事業の一環として電気試験所が取り組んだ、標準インダクタ作製作業において、ガラス製のボビンをアルミナ砥石で研削すると砥石摩耗が異常に大きく、必要な加工精度が出ないことに困っていたそうです。
工作物である(石英)ガラスよりもはるかに硬いはずのアルミナ砥石が、異常に摩耗するメカニズムを明らかにすることが研究テーマでした。
上司の助言により、複雑系のアルミナ砥石より純粋なアルミナ単結晶であるサファイアを用い、昼夜を厭わず実験を重ね、10年後に論文としてその成果を発表しました2),4)。
加工メカニズム
安永ら2)によれば、メカノケミカルポリシングはサファイアの摩擦界面における化学現象をもとに着想されたものであります。
摩擦や磨耗現象においては、接触する物質の形状や硬さなどの物理的な性質だけでなく、接触物質同志の固相反応や大気・水分などの雰囲気との化学反応など、種々の化学的作用が働いていることが知られています。
例えば、ダイヤモンドやアルミナ、炭化珪素などの非常に硬い材料が、鋼などの軟質材料との摩擦により磨耗する現象も、その一つと考えられており、工具磨耗の原因として良く知られています。
安永は、サファイア(Al2O3 単結晶)と鋼あるいは石英との磨耗実験において以下の反応生成物をX線回折手法により確認し、摩擦接触点における固相反応の存在を明らかにしました。
- Al2O3 + Fe(鋼)+ 5/2 O2 → Fe3O4-FeAl2O4 (固溶体)
- Al2O3 + Fe(鋼)+ 3/2 O2 → Fe2O3-Al2O3 (固溶体)
- 3Al2O3 + 2SiO2(石英) → 3Al2O3・2SiO2 (ムライト)
このような反応が進行する理由は、摩擦接触点局部において摩擦エネルギーによる高温・高圧が発生するためと言われています。
しかし、本当にそんな高温・高圧が発生しているのでしょうか?
そこで、一体どのぐらいの圧力が作用しているか推定してみました。
まず、接触という現象について曾田範宗先生は以下のように述べています3)。
「どんな表面加工、表面処理を行っても表面には凹凸が残るものである。こうした二つの面を向かい合わせて押し付けたときどんな現象が起こるだろうか。幾何学的平面を互いに押し付ければ、むろん全面が接触する。一方に凹凸があって、他方が幾何学的平面だったら、接触部に変形がないかぎり三点しか接触しないはずである。なんとなれば完全に同じ高さの凸部はないはずだから。両方の面に凹凸があれば若干複雑なかみあいをしようが、それでも接触点がそんなにたくさんできるとは思えない。
この固体表面の接触のイメージとしてかつてケンブリッジのパイ博士が『スイスをマッターホルンやアイガーもろとも裏返して、ヒマラヤ山系にかぶせたような状態』を想像すればよいと述べたのはいいつくして適切な表現である。要するに重要な点は、凹凸のある面は、見かけ上は広い面積を押し当てていても、本当に接触している面積は微々たるものだということである。3)」
この真実の接触面積とみかけの接触面積との比については、種々の方法で測定されています。
ですが、結論として真実の接触面積はみかけの接触面積の数百分の一から数万分の一に過ぎないというのが常識のようです。
通常のラッピングの加工圧は数百g/cm2、砥石ラッピングにおける加工圧は数㎏/cm2という場合もありますから、少なく見ても数十kg/cm2、最大で何と数十 ton/cm2と推定されます。
また、同著には摩擦面の温度についても以下の記述があります。
「実際の摩擦面の温度を実験で測定すると、普通の条件下でも驚くことに摂氏数百度から千度以上に達することがわかっている。・・・・・ 大切なことは、摩擦面の温度が鉄や鋼などでさえ溶けるような高温に達するという事実である。」
したがって、接触点局部は高温・高圧状態となり、通常では起こらない反応が進行するものと考えられます。
遊離砥粒方式によるメカノケミカルポリシング
更に、安永らは、遊離砥粒方式によりSiC,SiO2,Fe2O3,Fe3O4など種々の砥粒を用いてサファイアを研磨した結果についても考察しています。
サファイアよりも高硬度であるSiC を除いて、研磨量の多かったSiO2,Fe2O3,Fe3O4などは、メカノケミカル作用によるものと考えられるとし、その反応は以下のように推定されるとしています。
- 3Al2O3(サファイア)+ 2SiO2 → 3 Al2O3・2 SiO2 (ムライト)
- Al2O3(サファイア)+ Fe2O3 → 2FeO・Al2O3 ( スピネル) + 1/2 O2
- Al2O3 (サファイア)+ Fe2O3 → Fe2O3 – Al2O3 (固溶体)
- m Al2O3 (サファイア)+ Fe3O4 → 2FeO・(Al2O3)m・(Fe2O3)1-m (スピネル) + m Fe2O3
また、シリコン単結晶のメカノケミカルポリシングに適した軟質砥粒としてはBaCO3,CaCO3,Fe3O4などが4)、さらに窒化珪素のメカノケミカルポリシングに適した軟質砥粒としてはCaCO3,MgO,SiO2,Fe2O3,Fe3O4などが、別の研究者らにより報告されています5)。
ケモメカニカルポリシング
3つ目はケモメカニカルポリシングです。
上述の公益社団法人 精密工学会の調査研究分科会における整理法注1)によると、以下のようになります。
ケモメカニカルポリシングとは、加工雰囲気(※)の作用によってワーク表面に生じた反応生成物(酸化膜や水和膜など)を、砥粒の微小切削作用で除去する方法
※筆者注:乾式であれば空気や酸素雰囲気など、湿式であれば水あるいは研磨液など
代表的な事例は、ガラスのポリシングです。
加工メカニズムには、諸説があり、最も古い説は、1930年代に提唱された化学作用説と言われています6)。
下記図4で、ガラス表面の研磨モデルを示す通り、以下の流れで行われます。
- ポリシング液としての水の作用で、ガラス表面に軟質のケイ酸ゲル層が生じる
- 砥粒の微小切削作用によって軟質ゲル層が除去される
- 元のガラス表面が現れると、再び水の作用でケイ酸ゲル層が生成する
- このメカニズムの繰り返しにより、研磨が進行するという考え方1)
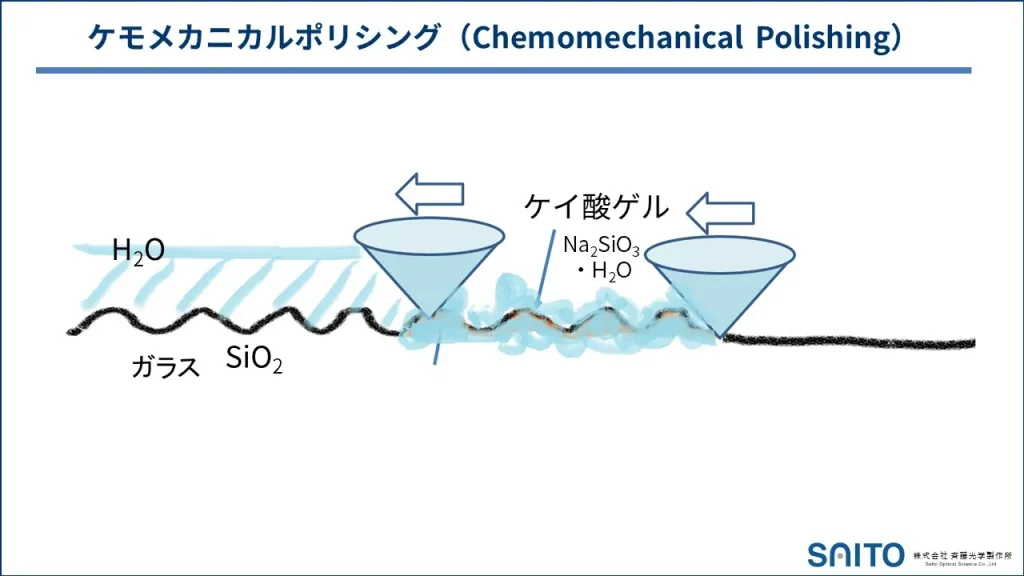
しかし、この説明だと最初のきっかけは、雰囲気と工作物との反応が先というように誤解されてしまい、少しミスリードになる懸念があります。
また、これでは砥粒は何であろうと関係ないということになりかねません。
実際には、砥粒の種類による違いはあります。
加工能率におけるセリア砥粒の優位性は明らかです。
それは、以前わが国で主に使われていたベンガラ(α-酸化鉄)を駆逐してしまったことは歴史が証明しています。
その優位性のメカニズムも、(セリウムの電気陰性度の強さからくる)セリウム原子と酸素原子との共有結合性の弱さに起因するなど、既にかなり解明されています7)。
そこで、きっかけは摩擦という機械的エネルギーにより、化学反応が励起されてできた生成物を砥粒で除去するとしたほうが分かりやすいのではないかと考えています。
すなわち、最初のきっかけはメカノケミカル現象であるということです。
メカノケミカル現象とは、固体、液体、気体に加えられた機械的エネルギー(圧縮、摩擦、せん断、曲げ、衝撃など)により、物質の物理化学的性質の変化が誘起されることと定義されます。
よって、表1では加工メカニズムとして、「研磨液と工作物との化学反応(水和、酸化)を砥粒の擦過作用により励起させ、できた反応生成物を砥粒でかきとる方法」という表現にしています。
分類 | 原理 | 事例 | |
---|---|---|---|
1 | 機械的ポリシング Mechanical Polishing(MP) | 微細砥粒による(塑性変形を主体とした)微小切削作用により鏡面化する。あるいは、摩擦熱により接触点局部を軟化させ、塑性流動により平滑化する | 具体例として微細アルミナによるアルミニウムディスクの研磨。微細ダイヤによるセラミックス、SiC、GaN単結晶のメカニカルポリシング(MP) |
2 | メカノケミカルポリシング Mechanochemical Polishing(MCP) | 工作物と、それより軟質な砥粒との固相反応を利用した方法で、砥粒と加工物とが接触する極微小領域での高温高圧により生じる反応物を砥粒でかきとる | コロイダルシリカによるサファイヤの仕上げ研磨が有名。微小領域でムライトが生成され除去される |
3 | ケモメカニカルポリシング Chemomechanical Polishing | 研磨液と工作物との化学反応(水和、酸化)を砥粒の擦過作用により励起させ、できた反応生成物を砥粒でかきとる | セリアによるガラスの研磨、SiC単結晶の酸化剤援用研磨など |
4 | ケミカル‐メカニカルポリシング Chemical-Mechanical Polishing(CMP) | 研磨液の化学的エッチング作用と砥粒の機械的切削作用とを複合させたプロセス | シリコンウェハの最終仕上げ(一次、二次、ファイナルポリシング)に採用されている |
5 | その他の新しいポリシング法 | 機械的エネルギー以外の磁気や電気エネルギーを付加して行う方法、工具と加工物が直接接触しないようにして歪の小さい加工を行う方法など | 磁気援用研磨、電気援用研磨、非接触研磨など |
このほかには、炭化ケイ素や窒化ガリウム、窒化ケイ素などの酸化援用研磨がケモメカニカルポリシングに含まれるのではないかと考えています。
これら炭化物や窒化物は共有結合性が強く、非常に硬くて、熱にも強く、化学的にも極めて安定です。
そのため、強力な酸やアルカリ、酸化剤に浸しておいても常温付近では全く反応しませんし、普通に研磨してもほとんど磨けません。
これらには、過マンガン酸塩などの強力な酸化剤を添加した研磨スラリーで表層を酸化物に変化させながら、研磨する方法が有効とされています。
このとき、酸化反応を砥粒の擦過作用により励起させ、反応生成物である柔らかい酸化物のアモルファス相を砥粒でかきとる方法であることからケモメカニカルポリシングに含まれると考えられます。
一方、須賀ら8)は窒化珪素や炭化珪素の仕上げ研磨に酸化クロム砥粒を用いて乾式でポリシングを行い、加工時に発生する加工生成粉を採取し、TEMやEDX、ESCAにより分析した結果、SiとOからなるアモルファス相が検出されたことを報告しています。
しかし、このアモルファス相にCrは検出されなかったことから、この加工においては加工物がそのままの状態で機械的に除去されるのではありません。
砥粒と加工物との接触点局部において、酸化クロムを触媒として加工物表面が酸化され、その結果生成されたSiO2主体の柔らかいアモルファス相が摩擦によって除去されたものと予想しています3)。
この場合は、ケモメカニカルポリシングではなくメカノケミカルポリシングに分類されると考えられます。
さらには、炭化ケイ素の仕上げ研磨に酸化クロム砥粒を用い、酸化剤(過酸化水素水や過マンガン酸塩)を併用した方法も、過去にはいくつか提案されていました9)。
これらを考えるとケモメカニカルとメカノケミカルの境目はあやふやになってきます。
しかし、いずれもメカノケミカル現象が基になっている点では同じであり、無理やり分類する必要もないのかもしれません。
ケミカル‐メカニカルポリシング
4つめはケミカル-メカニカルポリシング(CMPと略されることが多い)です。
この方法は、砥粒による力学的微小切削作用と、研磨液の化学的溶去作用との複合効果で材料を除去します。
すなわち、研磨液に工作物のエッチング(溶解)作用がある場合です。
材料が金属の場合は、酸や酸化剤を添加することで溶解が促進されます。
このとき、一旦溶解した金属イオンが水酸基(OH-)と結合して析出し、砥粒や研磨パッド表面に付着して阻害しないようにするには、研磨液のpHを十分低くしておくことや、金属イオンを捕捉する錯化剤などを添加しておくことが有効です。
シリコンやシリコン酸化膜の場合は、アルカリの添加により溶解が促進されます。
そのほか、ある化学種の溶解状態を予想するにはpHと酸化還元電位の関係を示した「酸化還元電位図」(プールベ線図)が参考になります。
代表事例は、シリコンウェハの仕上げ研磨(一次、二次、ファイナルポリシング)です。
中でも、シリカ砥粒をアルカリ溶液に懸濁した研磨液を用いる方法は、きわめて優れた平滑性と結晶性を有する鏡面が得られる方法として知られています。
使用される砥粒は10~80nmサイズのコロイダルシリカや酸化ジルコニウムなどで、加工液としてKOHなどの無機塩基や、様々な有機アミンが用いられます。
高能率を得るためには、加工圧、砥粒径・砥粒濃度などの機械的作用や、アルカリ濃度、pHなどの化学的作用、あるいは両者を同時に高めればよく、さほど難しくはありません。
一般的には、加工圧20~30kPa、pH10~13、温度20~25℃の条件で行われており、この条件におけるシリコンの加工能率は0.1~1μm/min程度です。
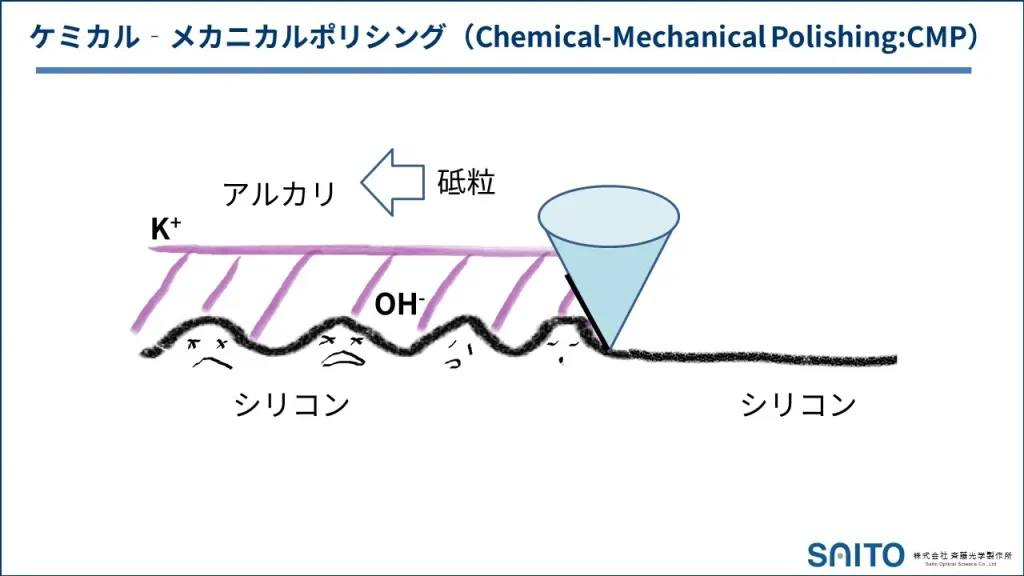
但し、機械的作用が強すぎると傷などの加工ダメージが入る危険性があり、逆に、化学的作用が強すぎるとダメージは少ないが表面に凹凸が生じ形状精度が劣化するなどの弊害が生じます。
したがって、機械的作用と化学的作用の両者のバランスをとることが最も重要となります。
以上はベアシリコンウェハに対して行われるCMPですが、シリコン半導体製造プロセスにおいてデバイスウェハ表面の凹凸、段差を平滑化、平坦化(プラナリゼーション)するために行われるポリシングもCMPと呼ばれます。
こちらはケミカル-メカニカル プラナリゼーション(Chemical-Mechanical Planarization)の略称となります。
半導体デバイスの高性能化は、配線の微細化や多層配線技術の発展により進められてきました。
ですが、そのプロセスにおいて、配線パターンの露光時に焦点深度以上の凹凸があるとパターン形状精度の劣化が生じます。
そのため、ウェハ表面の凹凸、段差を平坦化する処理技術が不可欠となり、1990年代以降CMPの導入が行われてきました。
研磨対象となる材料は、以下のようなものが代表的です。
- 層間絶縁膜などのSiO2・ポリシリコン
- 配線材料としてのW・Al・Cu
- 窒化ケイ素
最近ではルテニウムの登場など多岐にわたっており、各々の材料に応じた砥粒材料と添加剤の組み合わせが使用されています。
平坦化の取り代は、高々1μm程度と小さいため、砥粒の機械的作用と、添加剤の化学的作用とのバランスが大切なことです。
また、不純物による汚染や添加剤成分の分解などを防ぐため、砥粒にはナノメータオーダの粒径で、不純物を含まない高純度の金属酸化物系超微粒子が用いられています。
今後、半導体デバイスのさらなる高性能化のために、シリコンウェハのCMPは、ナノスケールの制御からオングストローム制御の世界へと移りつつあるとも言われており、加工技術のより一層の進展が求められます。
その他の新しいポリシング法
続いて、それ以外の磁気的エネルギーや電気的エネルギーを援用した研磨法のメカニズムについて解説します。
但し、「新しい」といっても40年くらいは経っていますのでご了承ください。
磁気的エネルギー援用研磨法
磁気的エネルギーを利用した研磨法は、大別すると以下2つの方法に分かれます。
- 磁性を持った砥粒を磁力でコントロールする方法
- 機能性流体(外部刺激により特定の性質や機能を示し、その性質や機能が工業的に応用できる流体の総称)を介して磁力により砥粒をコントロールする方法
ここでは機能性流体として磁性流体や磁気粘性流体を使用する研磨法について示します。
磁性研磨材を用いた磁気研磨法
磁性研磨材を用いた磁気研磨法10)とは、以下のように行う方法を指します。
- 磁場中に粒径30~40μm程度の磁性研磨材を充填して磁気ブラシを形成する
- その中で工作物を回転あるいは振動させる
- 工作物表面の研磨やバリ取り、エッジ仕上げなどを行う
その加工原理は、図6に示すように、直流磁界を作るN-S磁極間に磁性研磨材を充填すると、磁力線に沿って磁性研磨材がブラシ状に整列します。
そこに工作物を挿入すると、磁気ブラシは磁場により磁極間に保持されながら工作物表面を押し付けます。
このとき、工作物に回転および軸方向の運動を与えると、磁気ブラシと工作物との間に相対移動が発生し研磨が行われます。
ここで、磁性研磨材には高い磁化と高い研磨能力を兼ね備えた物質を使用しなければなりません。
そこで例えば、鉄にアルミナなどの砥粒をまぶしたような複合研磨材が用いられます。
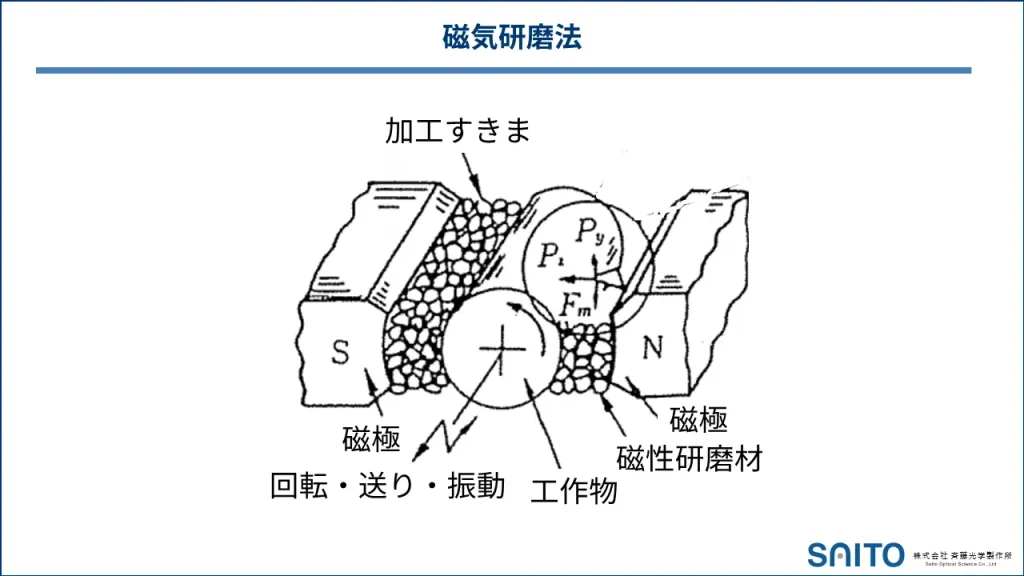
磁性流体( MF ; Magnetic Fluid)を用いた研磨法
磁性流体11)とは、直径が10nm程度の微細なマグネタイトなどの磁性粒子の表面に、界面活性剤をコーティングして水や油に安定に分散させた機能性流体です。
遠心力や磁場の印可に対しても固液分離せず、巨視的には磁性を有する均質な液体とみなすことが可能です。
この磁性流体に非磁性の砥粒を混ぜ込んで、図7のように永久磁石の上に載せると、磁性流体は磁場の強い方向に引き寄せられます。
それにより、非磁性砥粒は相対的に磁場の弱い方向(図では上の方向)に浮き上がり、高密度の砥粒層を形成します。
ここに工作物を押し当てて回転させれば、磁気浮揚力が加工圧として作用し研磨加工が実現されるわけです。
これが磁気浮揚研磨法12)です。
磁性流体の分散安定性を保障するためには、分散粒子の磁化に上限があるため高い加工圧が得られにくいという欠点がありました。
しかし、その後“浮き子“の力を利用した方法が開発され、セラミックス球の研磨にも応用されました13)。
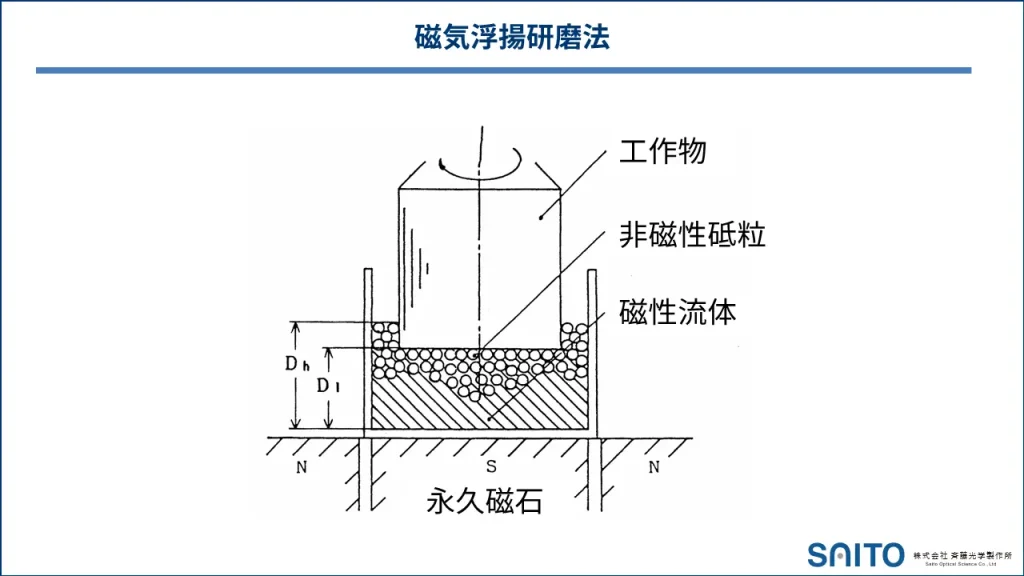
磁気粘性流体( MRF ; Magnetic Rheological Fluid)を用いた研磨法
磁気粘性流体とは、数μmに粒径をそろえた球状カルボニル鉄粉を界面活性剤でコーティングするなどして、シリコーン液に分散させた機能性流体です。
非常に磁化が高く、磁場の印可により、降伏応力を持ち、流動性がなくなり、見かけ上、固体のように振舞います。
それに砥粒を混合して循環し、図8のように構成した装置でMRF磁性流体研磨5)が行われます。
磁場を作用させた回転ホイール上に供給されたMRFは、磁場の作用で固体状になります。
そこに工作物であるレンズを押し当てることにより、せん断力で材料は除去されます。
MRFは常に循環しているので、新しい砥粒切れ刃が供給され、工具であるMRFの形状が崩れることはないため、加工能力は非常に安定しています。
また、砥粒は流体に支持されており、ナノレベルの加工単位を実現でき、形状精度と平滑性を向上させるとともに、前加工の加工変質層を除去できます。
この研磨法は、高精度レンズの形状修正研磨として重宝されています。
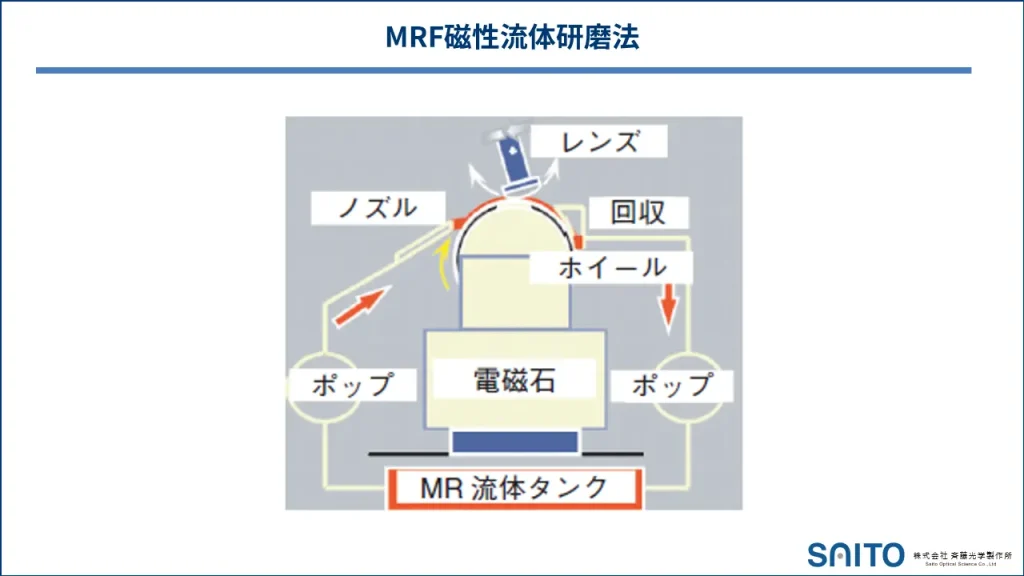
電気的エネルギー援用研磨法
電気的エネルギーを利用した研磨法には、電解溶出現象を利用した研磨法、電場(電界)中に配置した砥粒やスラリーの動きを制御する技術を利用した研磨法があります。
ここでは、その二つについて見ていきましょう。
その他には電気泳動現象を利用した研磨法などが知られています。
電解研磨法
この研磨法は、砥粒を使用しません。
塩化ナトリウムや硝酸ナトリウムなどの電解液中で、金属の工作物を正極とし、負極との間に直流電圧を印可します。
こうすることにより、工作物表面の金属が溶出する現象を利用して研磨を行う方法です14)。
平滑化するメカニズムとしては、以下の2つによるものとされています。
- 溶出の際、表面の微小凹凸部の凸部から先に溶出するため
- 溶出した金属イオンと電解液が混合し比重および粘度、電気抵抗の高いエマルションが生成し、凹部を被覆して溶出を妨げるため15)
この研磨法は、非接触加工であるため加工変質層は発生せず、きれいな光沢面が容易に得られますが、工作物表面の平坦性はあまり良くありません。
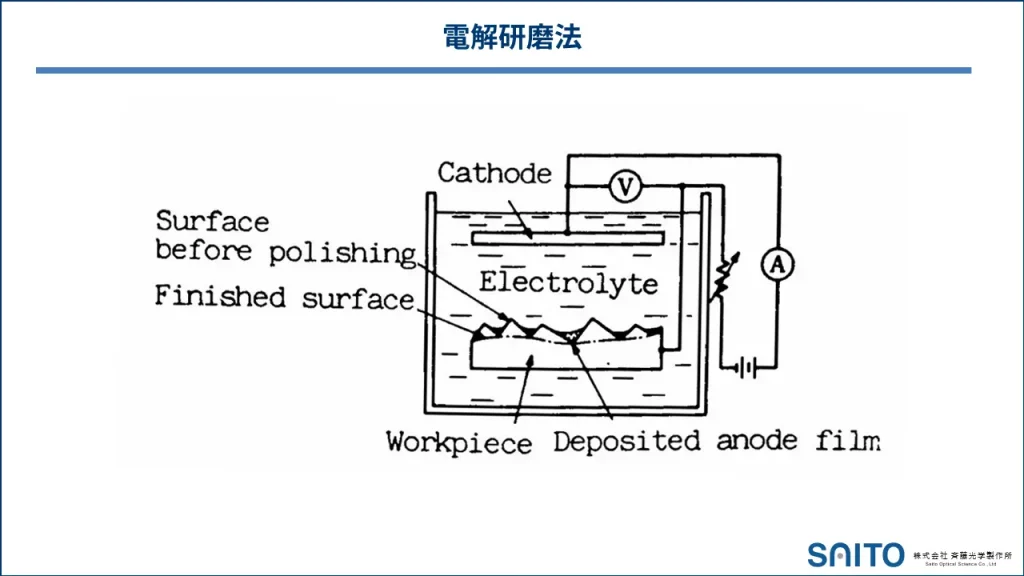
電解砥粒研磨法
この研磨法は、電解溶出現象による除去作用と、砥粒による機械的除去作用とを複合した研磨法です16)。
そのため、図10に示すように、装置としては回転円盤形電極工具を使用し、砥粒を混合させた電解液を噴流させて実施するなどやや複雑になります。
しかしながら、ステンレス鋼などの工作物に対し、広い面積を効率よく、平滑且つ平坦に仕上げるのには適しています。
電解砥粒研磨法で得られる仕上げ面粗さについては、電解溶出作用と砥粒による機械的作用とのバランスが重要です。
ある粒径の砥粒を使用する場合、仕上げ面粗さを最小にする最適電流密度が存在します。
この値以下の電流密度では、砥粒の引っ掻きによって工作物表面に現れた活性な表面に、速やかに不働態被膜が形成されます。
この部分の溶出が抑制されるため、良好な仕上げ面が得られるのに対し、高い電流密度では不働態被膜が形成されません。
砥粒の引っ掻きにより工作物表面に現れた活性な表面が連続して溶出するためピットが発生し、仕上げ面粗さは悪化します。
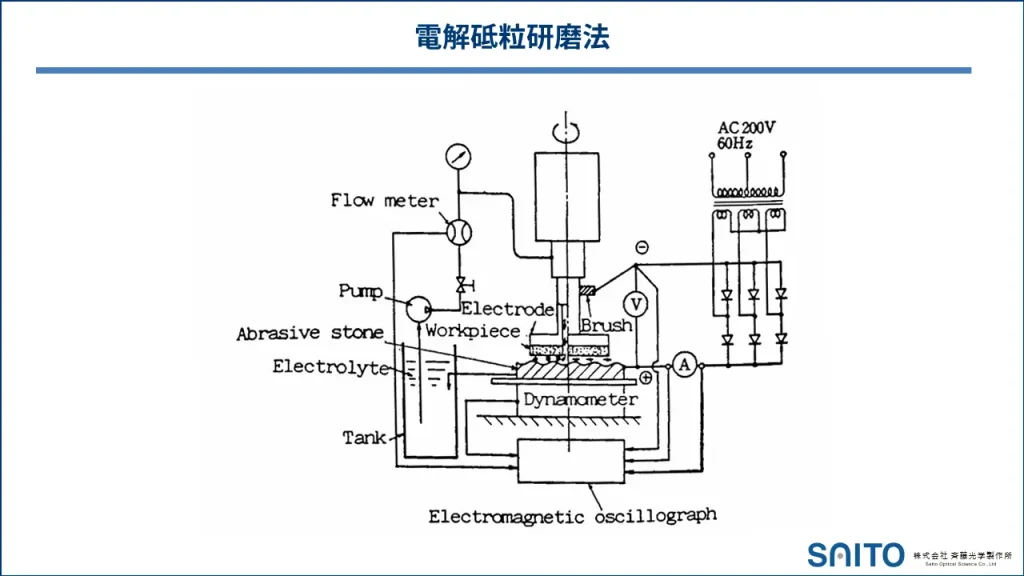
電界砥粒制御研磨法
ここで出てくる“電界”砥粒制御研磨法は、“電解”ではありません。
つまり、電解溶出現象とは関係ないのです。
Electric field の電界であり、加工領域に低周波高圧電界を印可してスラリーを機能性流体として用いる加工法が「電解砥粒制御技術」なのです。
但し、電解砥粒制御技術では、溶媒として絶縁性の油を用いる必要があります。
例として、比誘電率2.7の絶縁性シリコンオイルに比誘電率5.7のダイヤモンド砥粒を混ぜ込んだスラリーに低周波高電界を印可すると、砥粒が電界の極性変化に応答して活発に運動します(図11)。
それにより砥粒の飛散を抑制し、研磨領域に引き込むことにより良好な研磨を進めることが分かりました17)。
一方、コロイダルシリカなどの水ベースのスラリーは、水の比誘電率が80と砥粒より一桁も高く導電性もあることから、砥粒が電界の極性変化に応答することはありません。
そこで、制御の対象を砥粒ではなく「水」そのものとして展開したのが「電界スラリー制御技術」です。
水ベーススラリーの場合、水の比誘電率が約80なのに対して、空気の比誘電率は約1です。
このことから、電界により比誘電率の大きい水が、小さい空気の方向に引き込まれる方向に働きます。
これを利用して、低周波高電界の印可により水ベーススラリーそのものの運動を制御できるようになります。
それにより、種々の光学材料や半導体材料を効率よく研磨する、新たな手法として注目されるようになりました18)。

参考文献
- 1) 安永暢男:若手技術者へ贈る言葉「失敗を恐れずに」,砥粒加工学会誌,Vol65,No.10(2021)547.
- 2) 安永暢男, 今中治:メカノケミカル現象を応用した結晶材料の精密研磨法,セラミックス,9,4(1974)219.
- 3) 曾田範宗: 摩擦の話, 岩波新書(1971) 130.
- 4) 安永暢男:軟質パウダによるメカノケミカルポリシング法,機能材料,5,1(1985)24.
- 5) H.Vora,T.W.Orent and R.J.Stokes : Mechano-chemical Polishing of Silicon Nitride,J.Amer.Ceram.Soc., 65,9(1982)c140.
- 6) 安永暢男:研磨加工の基礎知識7:ポリシングの基本メカニズムと研磨事例、㈱イプロスTech Note編集部、5(2017).
- 7) 塙 健三 :ガラス用研磨材、NEWGLASS 、Vol.27,No.106,22(2012).
- 8) 須賀唯知:セラミックスの乾式メカノケミカルポリシング、日本学術振興会 「将来加工技術第136 委員会」第11回 研究会、Aprill.12.1991
- 9) メカノケミカル研磨方法及びメカノケミカル研磨装置、特開2001-205555.
- 10) 進村武男ほか:磁気研磨法の開発研究(第1報)-円筒仕上げへの応用-、昭和58年度精機学会講演論文集、(1983)、689.
- 11) 河田研治:磁性流体の製法と物性、トライボロジスト、vol41,No.6(1996)452.
- 12) 河田研治ほか:磁性流体を用いた磁気浮揚研磨法の研究(第1報)-磁性流体の研磨液としての特性と磁気浮揚研磨法の原理-、精密工学会誌、l53,6(1987)111.
- 13) 梅原徳次ほか:磁性流体研摩の研究(第1報)-球研摩における浮子の効果-、日本機械学会論文集(C編), 54, 503(1988)1599.
- 14) 大森整ほか:ELID研削とMRF磁性流体研磨を相乗した超精密複合プロセスの研究(第2報)、砥粒加工学会誌、50,6(2006)154.
- 15) 田中義信ほか:精密工作法(下)第2版、共立出版、(1982)151.
- 16) 田宮勝恒:電解複合加工法による金属の表面研磨、精密機械、50,3(1984)44.
- 17) 久住孝幸ほか:炭化ケイ素基板研磨のための電界砥粒分布制御研磨に関する研究、精密工学会誌、79,1(2013)87.
- 18) 千葉翔悟ほか:電解スラリー制御CMP技術を用いた酸化セリウム砥粒使用量低減研磨技術の開発、2012年度精密工学会春季大会講演論文集(2012)197.