SiC半導体基板加工における「原子間力顕微鏡を用いた極微小除去加工」とは?潜傷発生限界の調査についても徹底解説
2025/07/14
2025/08/15
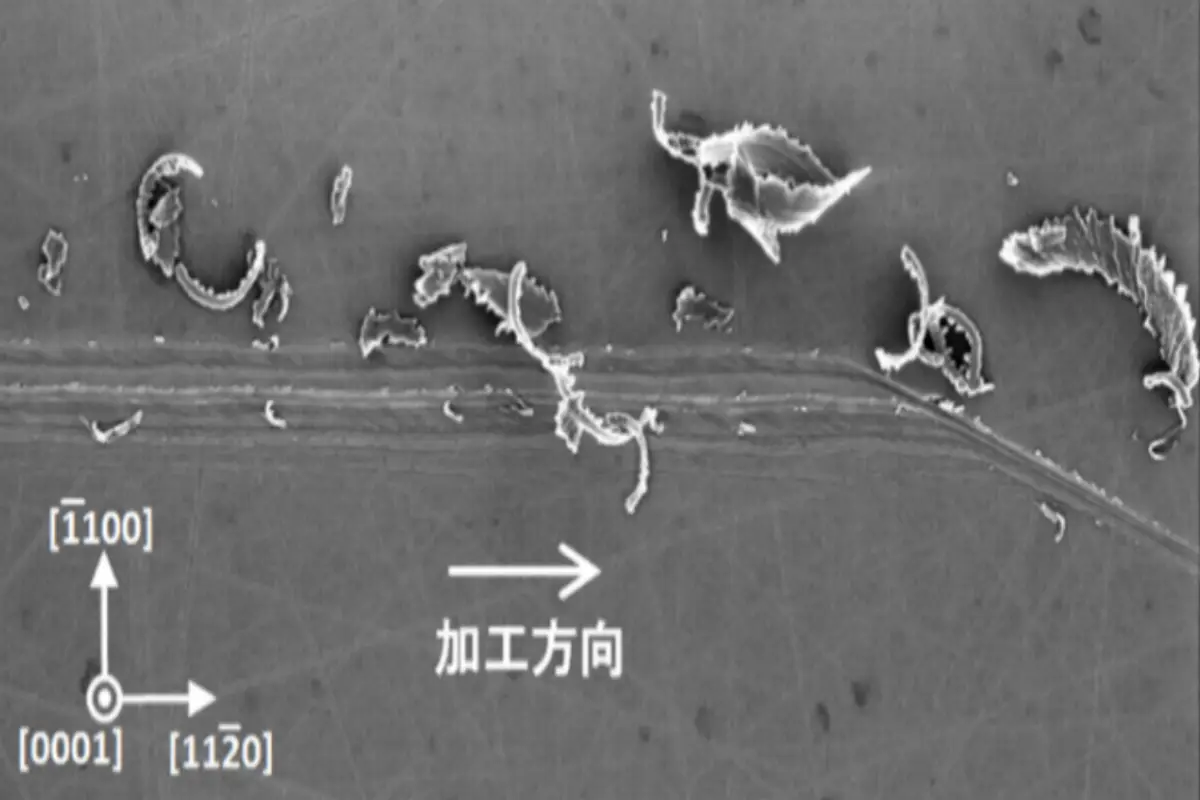
SiC半導体基板の加工においては極微小の傷や潜傷※など、表面及び表面近傍にわずかに残留する加工ダメージが、その後のエピ工程やデバイス工程に悪影響を及ぼすことが分かっています。
しかし、どのような傷や歪が問題になるか調査した報告はあります1)が、どの程度の力が砥粒の刃先に掛かるとSiCに傷や潜傷などのダメージが入るかについて定量的に調べたという報告はあまり見当たりません。
ここでは、筆者らが、潜傷が発生する限界荷重を調査する目的で、原子間力顕微鏡(AFM)を利用して、極微小な力をダイヤモンド刃先に作用させて基板表面を引掻きました。
本稿では、この方法を「AFM加工」と呼ぶことにします。
その加工痕を種々の顕微鏡やダメージ評価装置で観察し分析した報告2)~4)について解説します。
SiCウエハプロセスにおける異常傷の発生に関しては、「SiCウエハプロセスにおける異常傷の発生メカニズムと対策について実験結果を元に解説」の記事をご覧ください。
※潜傷とは研磨や加工の過程で表面には見えにくいが、材料内部や表層近くに生じる微細な損傷や欠陥のことを指します。
ここでは、2018年2月の「砥粒加工学会 次世代固定砥粒加工プロセス専門委員会 第77回研究会」で加藤智久氏(産総研)が述べた『CMP後に高分解能の表面形状測定でモフォロジーを持たないが、高分解能の放射線X線トポグラフなどで存在を確認できる加工痕』をSiC加工における潜傷の定義とします。
潜傷の本質は、結晶学的には積層欠陥の集まりと考えられます。
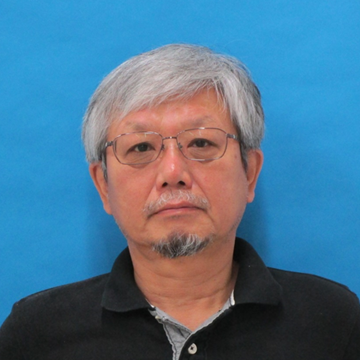
株式会社斉藤光学製作所技術顧問。専門が「研磨加工」と「微粒子分散」の技術コンサルタント。1976年、東北大学工学部を卒業後にタイホー工業株式会社 中央研究所にて磁性流体や研磨加工の研究に従事。1987年、東京大学より工学博士号(機械工学)を授与。2001年から3年間、東京大学生産技術研究所の客員教授。その後10年間は、研磨材メーカーの株式会社フジミインコーポレーテッド。さらにその後10年間は、国立研究開発法人 産業技術総合研究所 招聘研究員だった。
プロフィール詳細を見る原子間力顕微鏡(AFM)一体型の加工方法
原子間力顕微鏡一体型の加工装置5)は、現在、国立研究開発法人 産業技術総合研究所 北陸デジタルものづくりセンター所長である、芦田極氏によって1997年頃に開発されました。
芦田氏はシリコンウエハを用いて、極微小除去加工の原理実証を行いましたが、その装置をお借りしてSiCの極微小除去加工を行っています。
実験に使用したAFM装置の構成を図1に示しました。
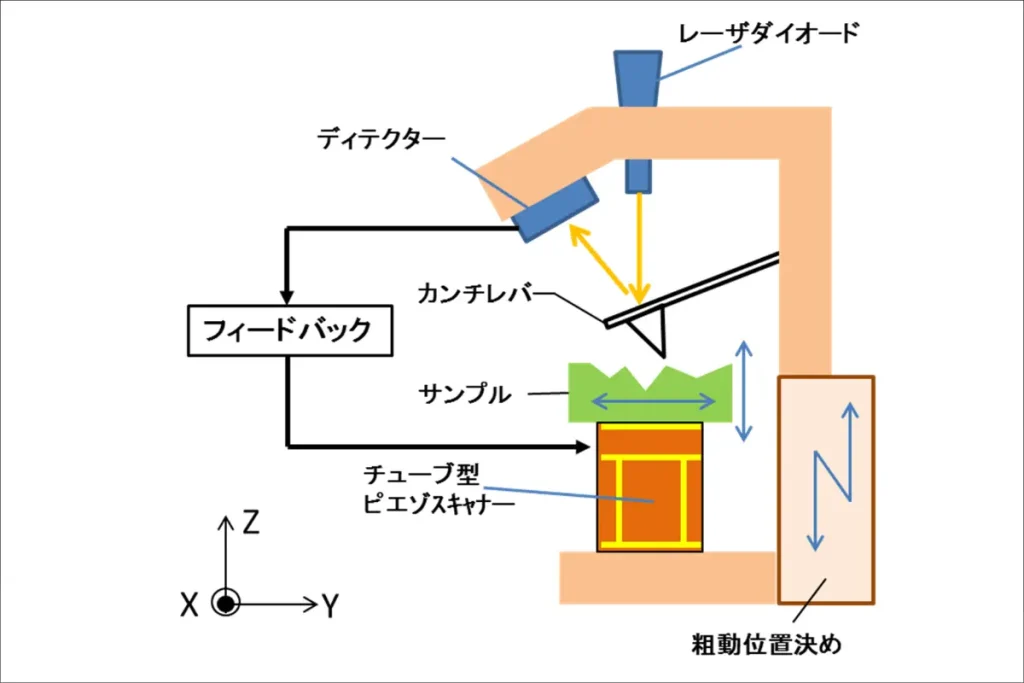
加工においては、接触モードAFMの原理を利用し、測定用とは異なる、加工専用のカンチレバーを用いました。
表1にその違いを示します。
カンチレバー | AFM測定用 | AFM加工用 |
---|---|---|
材質 | Si系 | ステンレス |
先端 | Si | ダイヤモンド砥粒 |
バネ定数(N/m) | 0.1 | 1000 |
荷重 | 1nN | 50μN~3mN |
加工用カンチレバーは、測定用カンチレバーよりもバネ定数を格段に高めたステンレス製のカンチレバーを用い、先端に粒子径20~30μmの工業用ダイヤモンド砥粒を接着し作製しました。
カンチレバー先端の拡大SEM画像を図2に示します。

加工用カンチレバーの大きな問題は、切れ刃形状のバラつきと摩耗です。
カンチレバー毎に切れ刃形状が異なり、形成される加工痕の形状に差が生じます。
また、同一のカンチレバーを用いた加工においても、加工実験を重ねるうちに切れ味が低下し、同じ加工条件でも加工痕形状が変化する場合があります。
そのため、実験は全て同じカンチレバーを用い、同じ日に連続で行いました。
荷重の設定においては、どの程度の垂直荷重で、どの程度の加工痕が形成されるかを把握することが重要です。
そこで、芦田氏の論文を参考にヘルツの弾性接触理論を用いて、ダイヤモンド切れ刃の垂直荷重とSiCの加工痕サイズの関係を見積もりました。
その結果、加工痕深さ1~100nmの加工を行うために必要な垂直荷重はSiと同様に1~1000μN(AFM測定の千~百万倍、触針式粗さ計の千~百万分の一)と計算されたため、Si加工用のカンチレバーをそのまま使用できると判断し実験を行いました。
AFM機構では切れ刃をカンチレバーに固定し、カンチレバーのたわみ量、すなわち切れ刃に負荷する荷重を一定に制御して切込みを与えます。
また、送り機構に相当するチューブ型スキャナは直線運動を行わず、加工面の形状に倣った動作をします。
つまり、砥粒加工における圧力切込み方式に似た形態を再現できるのです。
図3にAFM加工により生じた切りくずのSEM画像を示しました。

切りくずの形状は若干カールしており金属などの延性材料が塑性変形した切りくずのように見えます。
切れ刃の先端部のみで材料と接触し、すくい角が負であっても、切りくずがすくい面に沿って上方へ排除されずに、刃の側方へ逃げる可能性が高くなるのです。
そのため、細長い切りくずが生じるものと考えられます。
AFM加工の実験方法
実験条件を表2に示します。
荷重 | 加工面 | 引掻き方向 | 刃先送り速度 | ダメージの評価方法 |
---|---|---|---|---|
50μN 100μN 200μN 300μN 500μN 700μN 1000μN | 4Hn-SiC Si面 C面 | <-1100> <11-20> <1-100> <-1-120> | 10μm/s | CDIOM SXRT MEM TEM SEM |
事前に、荷重500~3000μNで加工してみたところ、大半の加工痕の下にはダメージが存在していました。
そのため、潜傷の発生限界を探るという目的には荷重が大きすぎると考え、荷重を50μNから1000μNまでの範囲に設定しました。
また、基板の表裏(Si面とC面)について、<-1100>、 <11-20> 、<1-100> 、<-1-120>の4方向を各々実施しました。
加工パターンは図4に示すように50μNから段階的に荷重を増やし、1000μNまで合計7本のラインを描くようにプログラミングしています。
図の破線は荷重をかけないで移動するラインを示します。

AFM加工によるダメージの評価結果と考察
ダメージの評価は全ての実験条件について(1)共焦点微分干渉顕微鏡(CDIOM)、 (2) 放射光X線トポグラフィー(SXRT)、(3) ミラー電子顕微鏡(MEM)で行いました。
これらのダメージ評価方法のイメージを図5に示します。

CDIOMは、レーザー光を点状に試料に照射し、ピンホールを使って焦点面以外の信号を除去することで、非常に高いZ軸分解能を実現します。
また、SiCのような透明試料でも詳細な構造を可視化できます。
SXRTは、非破壊で結晶内部の欠陥(転位、積層欠陥など)を高感度・高分解能で可視化する手法です。
X線の侵入深さが数十μmまでの深いダメージを見られます。
特にSiCやGaNウエハの結晶欠陥評価に有効です。
但し、特殊な大型の放射光施設が必要で、リアルタイム性には劣ります。
今回も九州シンクロトロン光研究センターで行いました。
MEMは、反射電子を利用して表面の構造を観察する電子顕微鏡で、表面極近傍(数nm以下)の非接触・非破壊観察が可能です。
実寸の傷ではなく、欠陥に寄ってきた電荷の集合体を見ているため、表面ポテンシャルの差、わずかな高低差でもコントラストが高い画像が得られます。
実験結果を表3に示します。
加工荷重(μN) | |||||||||
---|---|---|---|---|---|---|---|---|---|
面 | 加工方向 | Ex.No. | 1000 | 700 | 500 | 300 | 200 | 100 | 50 |
Si面 | (1)<-1100> | 1204-1 | ● | ● | ● | ● | ● | ● | - |
■ | ■ | ■ | - | - | - | - | |||
1204-5 | ● | ● | ● | ● | - | - | - | ||
- | - | - | - | - | - | - | |||
(2)<11-20> | 1204-6 | ● | ● | ● | ● | - | - | - | |
- | - | - | - | - | - | - | |||
1204-2 | ● | ● | ● | ● | ● | ● | ● | ||
■ | ■ | ■ | - | - | - | - | |||
(3)<1-100> | 1204-3 | ● | ● | ● | ● | ● | ● | - | |
■ | ■ | ■ | - | - | - | - | |||
(4)<1-120> | 1204-8 | ● | ● | ● | ● | ● | ● | ● | |
■ | ■ | ■ | - | - | - | - | |||
1204-4 | ● | ● | ● | - | - | - | - | ||
- | - | - | - | - | - | - | |||
C面 | (1)<-1100> | 1204-9 | ● | ● | - | - | - | - | - |
- | - | - | - | - | - | - | |||
(2) <-1-120> | 1204-10 | ● | ● | ● | ● | ● | - | - | |
■ | ■ | ■ | - | - | - | - | |||
(3)<1-100> | 1204-11 | ● | ● | - | - | - | - | - | |
- | - | - | - | - | - | - | |||
(4)<11-20> | 1204-12 | - | - | - | - | - | - | - | |
- | - | - | - | - | - | - |
●:MEMで検出 ■:SXRTで検出 -:未検出
表中では、各荷重で引掻いた傷が検出できる場合について、MEMは「●」、SXRTは「■」で示しています。
まず、CDIOMでは全ての実験条件において傷が全く検出できませんでした。
しかし、SXRTやMEMでは表面下の情報として線状の欠陥が見えているものもあります。
以下、図6に示しました。
-1024x683.webp)
これらは冒頭で定義した「潜傷=表面にモフォロジーを持たないが、結晶内部に欠陥が確認できる加工痕」と考えられます。
しかし、n=2の実験に再現性がとれておらず、Si面とC面の差や、結晶方位(引掻き方向)による差異などは明確とはなりませんでした。
次に行ったのは、破壊検査です。
比較的明瞭に見えているEx.No1204-2の加工痕(Si面、<11-20>方向)について断面TEM観察を行いました。
実施したのは50μN,300μN,1000μNの加工痕です。
観察の結果、1000μNおよび300μNの条件では、逆三角形のダメージが観測されており、応力が大きいほどダメージが深い傾向も確認できました。
図7に内容を示しています。
-1024x683.webp)
50μNの条件では、SiC内部に結晶欠陥を伴うダメージが観測されていないことが判りました。
以上の結果から、ある荷重で加工痕が見えているかどうかを装置ごとにまとめたのが、表4になります。
荷重(μN) | ダメージ評価方法 | |||
---|---|---|---|---|
CDIOM | SXRT | MEM | 断面TEM | |
50 | × | × | △ | × |
100 | × | × | 〇 | ー |
200 | × | × | 〇 | ー |
300 | × | × | 〇 | ○13nm |
500 | × | 〇 | 〇 | ー |
700 | × | 〇 | 〇 | ー |
1000 | × | 〇 | 〇 | ○38nm |
【凡例:ダメージ判定】
✕:全く観察されない
△:一部観察される
○:明瞭に観察される
この表から、潜傷の発生限界荷重を推定すると、非破壊検査であるCDIOMでは、50~1000μNでは表面の傷は確認できないことから、全て潜傷あるいはそれ以下のレベルの加工痕と言えます。
また、SXRTの結果から500μN以上の荷重でダメージが確認できていることから、潜傷の発生限界荷重としては一応この辺りが有望と考えられます。
しかし、破壊検査ではあるものの、断面TEMで300μNにおいて潜傷が確認されていることから、300μN辺りを発生限界荷重とすべきかもしれません。
一方、MEMでは100μN辺りから1000μNに至るまで、明瞭に加工痕が確認できました。
また、表面の測定画像から内部の欠陥情報もある程度推定できることが判っています。
そこで、あらかじめ「潜傷の標準試験片」のようなものをAFM加工などで作成しておき、「製品となるウエハと標準試験片とをMEMで比較評価することにより良否判定する」という方法も可能になると考えられます。
まとめ
今回は、AFM加工という特殊な方法を用いて、SiCに潜傷が発生する限界荷重を調査した報告について解説しました。
今回の実験では、300~500μN(約30~50mgf)辺りに潜傷の発生限界があるという結果となりました。
耳かき1杯の粉の重量が20~30mgと言われていますので、わずか耳かき1~2杯の粉末位の荷重でダメージが入るということになり、あらためてSiCの仕上げ研磨には細心の注意が必要ということがお分かりいただけるでしょう。
参考文献
- 佐々木ら,4H-SiC(0001)Si 面上の局所的ステップバンチング発生原因の解析,応用物理学会 第60回春期学術講演会予稿集 29P-PB4-4.
- 河田ら,AFMを利用したSiC単結晶の極微小除去加工,先進パワー半導体分科会誌「第3回講演会 予稿集」,(2016)164.
- 河田ら,AFMを利用したSiC単結晶の極微小除去加工(第2報),先進パワー半導体分科会誌「第4回講演会 予稿集」,(2017).
- 河田ら,AFM を利用した SiC ウエハ表面の極微小除去加工-加工痕の SEM、TEM、MEM、SXRT 観察による潜傷発生限界の調査-,ABTEC2019.
- 芦田ら,原子間力顕微鏡一体型加工評価装置の開発(加工用カンチレバーの開発),砥粒加工学会誌(1997), 41(7), 276-281.